Pschorr Bräurosl Oktoberfest 4.0
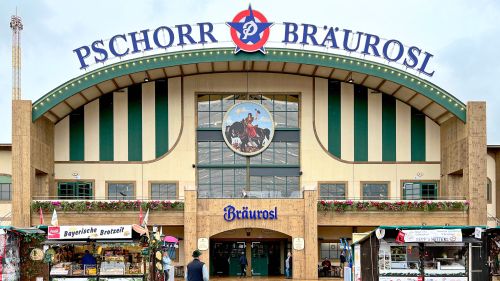
Tradycyjny Bräurosl opiera się na nowoczesnych rozwiązaniach automatyki w systemie rozlewania.
IO-Link zabezpiecza dostawy piwa do namiotu na festiwalu Oktoberfest w Monachium
Tradycyjny namiot Pschorr Bräurosl był już techniczną atrakcją w 1901 roku, kiedy został po raz pierwszy ustawiony na Oktoberfest: był to pierwszy namiot z oświetleniem elektrycznym. Ponad sto lat później, w 2011 roku, pod namiotem zainstalowano linię do nalewania piwa. Pomogło to zoptymalizować dostawy festiwalowego piwa do namiotu, od logistyki nocnych dostaw po pożądaną jakość i wydajne dostawy do poszczególnych barów. Kiedy namiot został przeprojektowany w 2019 r., Grupa Browarów Paulaner, do której należy marka Hacker-Pschorr, skorzystała z okazji, aby jeszcze bardziej zoptymalizować tę linię pierścieniową.
Do nalewaka przez linię pierścieniową
Linia pierścieniowa piwa jest centralnym elementem technologii dozowania Pschorr Bräurosl. Została ona zainstalowana po raz pierwszy w 2011 roku i przebiegała pod ziemią pod namiotem. Zasila sześć punktów poboru festiwalowym piwem z kontenera technicznego z trzema centralnymi zbiornikami piwa o pojemności 28 000 litrów. Pomimo wszystkich zalet, konserwacja tego rurociągu zawsze stanowiła wyzwanie dla inżynierów browarnictwa. Dlatego też, podczas przeprojektowywania Pschorr Bräurosl, browar zdecydował się przenieść linię piwnego pierścienia do samego namiotu. Przebiega ona teraz pod balkonem.
Aby zapewnić, że piwo dociera do kranów w idealnej temperaturze około 1°C, zainstalowano izolowaną próżniowo linię, która dostarcza piwo do kranów w najwyższej możliwej jakości.
Koncepcja technologii rozlewania w namiocie festiwalowym Bräurosl została opracowana przez Uwe Daebela, dyplomowanego inżyniera browarnictwa w Grupie Browarów Paulaner, który miał okazję zebrać doświadczenie techniczne w podobnych projektach w przeszłości.
Przepływomierze elektromagnetyczne mierzą dokładnie ilość napoju na poszczególnych nalewakach. Inne czujniki wykrywają różne wartości temperatury, przewodności i ciśnienia w systemie. Wszystkie te zmierzone wartości są wykorzystywane przez gospodarza festiwalu do oceny ilości podczas działania systemu i co bardzo ważne do prognozowania ilości piwa, które muszą być dostarczane każdej nocy przez cysterny. To oparte na czujnikach ilościowe i jakościowe monitorowanie przepływu piwa jest jedynym sposobem na zapewnienie gościom pięknie nalanego, a przede wszystkim świeżego piwa festiwalowego przez cały czas podczas 16-18 dni Oktoberfest.
Zarządzanie danymi przez IO-Link
Dla planistów szybko stało się jasne, że potrzebna jest potężna infrastruktura danych do gromadzenia ogromnej ilości danych z czujników i przesyłania ich w pakietach do centralnego kontrolera. Wybór padł na technologię elektroniczną IO-Link firmy ifm. Ponieważ technologia ta była wciąż nowa dla firmy, której zlecono projekt, specjalista ifm zapewnił szkolenie zorientowane na potrzeby na wczesnym etapie projektu. Podczas fazy wdrożeniowej firma ifm zapewniła również szybkie i osobiste wsparcie w miarę pojawiających się pytań.
Zaawansowana technologia przetwarza ponad sto wartości pomiarowych z czujników za pośrednictwem kilku zdecentralizowanych masterów IO-Link i przesyła je przez Profinet do centralnego sterownika PLC. Na ich podstawie sterownik PLC koordynuje wszystkie procesy dostarczania napojów. Jednocześnie wszystkie istotne dane są przesyłane do chmury i analizowane w czasie rzeczywistym. Odchylenia procesowe są natychmiast wskazywane, dzięki czemu można w odpowiednim czasie podjąć środki zaradcze. Zapewnia to maksymalną niezawodność dostaw i jakości.

Czujniki przepływu dokładnie monitorują natężenie przepływu w każdym nalewaku.
IO-Link jako standard niezależny od producenta
Do każdego z masterów AL1403 IO-Link ifm można podłączyć do 8 czujników i elementów wykonawczych. Sygnały binarne mogą być również przesyłane przez porty I/O tych modułów, co dodatkowo upraszcza instalację w Bräurosl.
Podsumowując, technologia IO-Link jest idealnym wsparciem dla efektywnego działania złożonej technologii Bräurosl. Ogromna korzyść: Bez żadnych problemów można podłączyć nie tylko czujniki ifm, ale także czujniki innych producentów. Dzięki oprogramowaniu ifm moneo configure SA wszystkie podłączone czujniki można konfigurować i diagnozować z centralnej lokalizacji poprzez zdalny dostęp. Umożliwia to nie tylko łatwą konfigurację, ale także szybką diagnostykę w przypadku awarii.
Higienicznie zaprojektowane moduły obiektowe IO-Link z serii Food (spożywczej) są przeznaczone do użytku w trudnych warunkach. Umieszcza się je dokładnie tam, gdzie generowane są dane z czujników, zarówno w samym namiocie, jak i bezpośrednio w kontenerach chłodniczych, w których przechowuje się napoje bezalkoholowe w beczkach.
Zdecentralizowana instalacja znacznie zmniejszyła złożoność instalacji. Eliminuje to również typowe przeszkody, takie jak problemy z potencjałem lub zakłócenia wartości analogowych. Łączenie sygnałów związanych z czujnikami oferuje nieocenione korzyści w porównaniu z konwencjonalnym oddzielnym okablowaniem wszystkich czujników, zwłaszcza w dużych instalacjach tymczasowych z sieciami o długości kilkuset metrów.

Zdecentralizowane mastery IO-Link zbierają różne sygnały czujników i przesyłają je w wiązkach przez Profinet do centralnego sterownika.
Wniosek
Dzięki technologii IO-Link ifm znacznie łatwiej i szybciej jest ponownie zdemontować złożoną technologię po zakończeniu Oktoberfest i przechowywać ją do następnego użycia, zapewniając jednocześnie, że będzie działać niezawodnie. Co więcej, zmiany lub rozszerzenia można łatwo wdrożyć. Interfejsy IoT zintegrowane z masterami IO-Link umożliwiają również analizę danych i przesyłanie ich bezpośrednio do IT lub chmury, z pominięciem PLC.
Dla firmy, która otrzymała zlecenie, korzystanie z IO-Link stanowiło znaczną ulgę. Jedno jest pewne: Zalety IO-Link będą niezbędne w kolejnych projektach.