- Encoders
- Applications
Application examples
Rotational, height and linear movements
Example: Height determination of lifts using an absolute multiturn encoder on a toothed wheel.
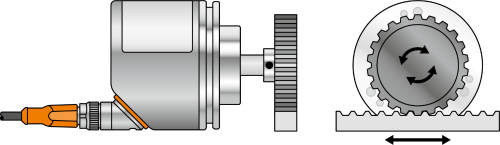
Rotational and distance movements
Example: Spindle adjustment for precise positioning using an absolute multiturn encoder.
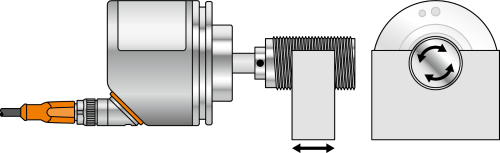
Rotational and linear movements
Example: Linear measurements using an incremental encoder on a measuring wheel.

Rotational movement for speed determination
Example: Rotational speed detection of motors using an incremental encoder.

Rotational movement for position determination
Example: Positioning of rotary indexing tables for different production steps using an absolute singleturn encoder.
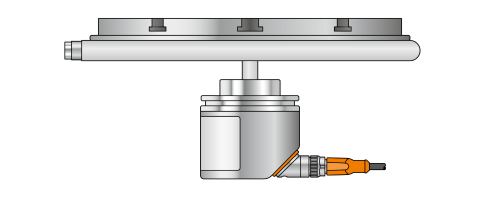
Rotational movement for angle determination
Example: Steering angle detection for operating AGVs using an absolute singleturn encoder.

Use on forklifts and AGVs
The compact IO-Link multiturn encoders are particularly suited for use in AGVs and forklifts. The small 36 mm diameter housings allow for a small footprint installation. They can be connected to all common controllers using an AL1xx type IO-Link master and a standard M12 cable. This makes expensive fieldbus cables that have to be assembled obsolete.
Fork width adjustment
The width of a forklift fork is adjusted by means of a gear wheel and rack. The absolute encoder installed on the gear wheel determines the exact fork width and reports it to the controller.
Fork height
To precisely determine the fork height, the absolute encoder detects the revolutions on the wire rope pulley and transmits this information to the display unit and controller.
Drive wheel and steering
Two encoders are installed in the steering system: While one precisely determines the steering angle of the wheel, the other sits on the shaft of the drive motor, providing two process values: the rotational speed in min-1and the exact wheel position.
Other machines
Sheet cutting on a punching machine
An infinite sheet of metal runs through the machine and is punched to defined lengths. A photoelectric sensor looks at the front edge of the sheet and starts the counting process by setting the encoder on the measuring wheel to zero by means of a switching signal. This direct reset input on the ifm encoder means there is no PLC involvement. Even in rapid processes, time delays and resulting mechanical displacements are effectively avoided. In addition to length measurement, the IO-Link encoder provides the belt speed as a second measurement value.
Fan monitoring
Installed on the fan shaft, the encoder not only monitors the speed. It also records the operating hours to help optimise maintenance intervals.
Thermoforming packaging machine
The conveyor belt must run synchronously with the fed film. Encoders installed on measuring wheels precisely monitor the speed and report even the smallest deviations to the controller.
Roller conveyor
Long conveyor lines consist of individual, separately driven segments. To prevent jams or collisions, encoders are installed on the axes of the drives to ensure that they all run at the same speed.
Overhead conveyor
In the slaughterhouse, the half carcasses hanging on hooks are transferred from the overhead conveyor to the storage belt. To ensure a smooth transfer, the two systems must operate absolutely synchronously. Encoders on both systems ensure that the systems are in perfect sync. Thanks to their V4A housing and protection rating IP68/69K, the encoders can withstand even the extreme cleaning processes employed in slaughterhouses.