- Automotive Industry
- Joining
Optimized joining processes during Body-In-White improves quality
The quality of a vehicle in the body-in-white stage directly impacts its safety, durability, and performance. Maintaining high quality is essential, as defects here will accumulate and result in costly scrapped product further into the manufacturing process. Automation in the BIW stage ensures high quality standards are met, while improving efficiency. Sensors, robotics, and integrated software provide high-precision inspection for enhanced quality checks and automated tracking systems for traceability throughout the process.
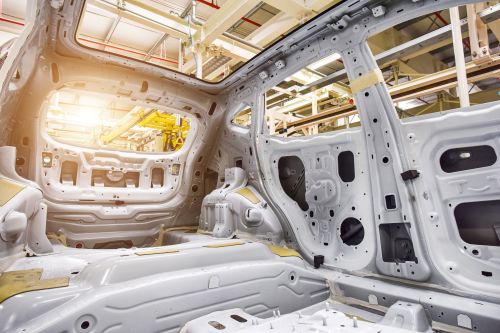
Enhanced structural integrity:
A well-executed BIW process with comprehensive inspection stations ensures the vehicle's structural strength, validating its safety and reliability for the consumer.
Improved production efficiency:
Streamlined BIW processes lead to faster, more efficient production lines, which are essential to staying competitive in the market.
Customization and flexibility:
Advanced BIW techniques allow for greater design flexibility, enabling manufacturers to efficiently produce a wide range of models to meet varying customer demand and preferences.
Using advanced technologies, BIW process engineers meticulously design and assemble the car body, ensuring every component aligns with stringent quality and safety standards. Increasing machine vision inspection during this phase has immediate ROI, as identifying defective parts prevents them from continuing further down the production line and escalating scrap costs. As the joining process becomes increasingly complex with different materials, it is extremely important to monitor these processes to ensure high quality.
Joining processes in the Automotive Industry
Joining processes have evolved over time as consumer trends and regulatory demands have changed. No longer just relying on welding steel components, manufacturers now have to manage multifaceted processes with diverse steps in production:
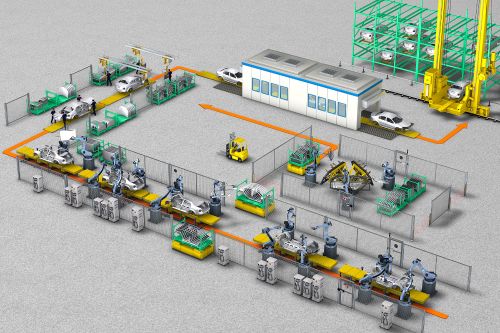
- BIW in EV battery production: Manufacturers have adapted BIW processes for the unique requirements of electric vehicles, including battery housing integration. Use connected flow or level sensors to ensure battery cooling loops have the appropriate amount of glycol, and track the date and time of this step for traceability requirements.
- Lightweight BIW designs: Implementing lighter materials for greater fuel efficiency means introducing new techniques of joining that need to be monitored. Add connected pressure and level sensors to adhesive equipment to implement automatic refills or to receive alerts that help you avoid unplanned downtime.
- Robotic automation in BIW: Implementing robotic riveting systems for BIW assembly enhances both quality and speed. Laser distance sensors ensure a continuous rivet feed into automated Self-Piercing Rivet (SPR) robots. When machine vision inspection solutions are more affordable and easier to integrate, you can add more inspection points to ensure high quality products and to reduce scrap.
Is investing in additional error-proofing during BIW worth It?
Cost
Increasing additional inspection technologies or points of inspection during assembly has a reputation for being costly or complex. But, most manufacturers do not need complex camera systems that require specially trained personnel to maintain and troubleshoot. Investment in new, more affordable technologies eliminates the need for complex training and provides greater flexibility when reconfiguring manufacturing lines.
Results
Investing in new inspection technologies ultimately reduces costs. When you can implement lower cost alternatives that still provide robust performance, it results in additional points of inspection throughout production. The results include improved efficiency, reduced material waste, and enhanced product quality. These improvements lead to cost savings over time and a stronger market position, in addition to the reduced hardware costs.
Inspection technologies in BIW
Hardware
There are many error-proofing technologies available today to serve a wide range of inspection applications. In order of complexity, common technologies include:
-
Time of Flight laser distance sensor: high performance with metallic, rounded, or matte targets makes the OGD series sensor extremely reliable for part presence checks when compared to traditional CMOS triangulation. The significant cost reduction means lower initial investment costs.
-
Vision sensors: performs high quality contour checks, color sortation, part seated checks, part orientation checks, and other more complex inspection applications without the cost of an overengineered vision system.
-
IO-Link Image-based code-reader: simple teach button setup reduces implementation and integration time of Optical Character Recognition (OCR) inspection, and sends barcode scan data through an IO-Link master directly to ignition or higher level software systems for better traceability at every step of production.
Software
moneo|software acts as an intermediary between your production line and ignition SCADA system. It receives sensor data over IO-Link, and ensures that data is processed before sending it to higher level software systems. It provides a robust solution for traceability systems.
Using IO-Link technology, moneo|software and vision system technologies can record historical logs of part inspection. This data can be sent to higher-level software systems without interfering with machine control or PLC functions. This gives greater visibility and traceability to workers for long-term storage, planning and optimization, without compromising production processes.
Gain a competitive edge
Incorporating robust inspection technologies in BIW processes helps you lead the way in automotive manufacturing excellence. You gain a competitive edge by ensuring the production of high-quality, innovative vehicles.
Learn more about how ifm’s inspection solutions can help you meet evolving market demands and customer expectations.