- Discover IO-Link
- Application solutions
IO-Link application solutions
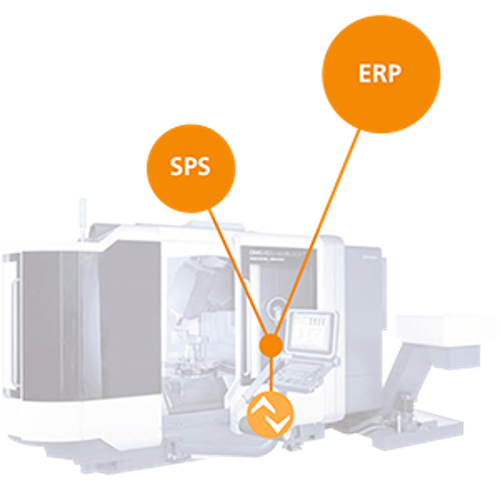
IO-Link with IIoT technology provides process transparency and more data to ensure you operate at peak efficiency. Browse some documented solutions below or read customer stories and use cases.
TW non-contact temperature sensors
Unable to see through scale, smoke or steam in a steel mill to determine proper temperature or position?
There are always smoke, steam, and cracks or breaks between the scale in a steel mill. ifm's TW infrared non-contact temperature sensor picks out the hottest temperature in a specified time window and sends that value to the PLC over IO-Link.
The acyclic (on demand) parameter is called "peak hold function" and it allows the user to set a time window from 0...600 seconds and "hold" the highest temperature measured.
Need to change emissivity on the fly?
For the most accurate temperature measurements, you need an accurate emissivity value. If you change materials on your line (steel to brass, for example), you must change the emissivity value in the sensor's configuration. ifm's TW sensor allows this setting to be changed from the PLC, reducing downtime on changeovers.
LDL conductivity sensors
Media transition detection made more accurate and affordable
Using IO-Link, the resolution of the conductivity value is the same throughout the measuring range. A typical CIP process uses chemicals with high conductivity and rinse water with low conductivity. When using an analog output, the signal is spread out over a greater range, reducing the ability to detect small changes in conductivity. This can lead to residual amounts of chemicals going undetected in rinse water or products.
One integrator who works with many dairies was able to improve the overall efficiency of their CIP skids by taking advantage of IO-Link. With more points in the system, the amount of chemicals used, the time required for a cleaning cycle, and the amount of rinse water are all optimized.
Utilizing the IoT port of ifm's IO-Link masters, they were able to pull all process data into their servers and remotely monitor the process.
SD compressed air meters
Compressed air is not free
Compressed air leaks often waste 20 - 30% of your compressor's output. A ¼" hole can leak up to 62 cfm at 100 psi and the cost can go unnoticed.
The SD flow sensor continuously monitors the flow rate, volume, pressure and temperature of compressed air. Simply mount in a zone, production line, or machine drop to quickly identify leakage and consumption values. The integrated pressure measurement assures actuators are operating at maximum efficiency and eliminates the need for a separate instrument.
IO-Link technology allows you to visualize real-time data. Trends over time, consumption changes, process value changes, etc. can all indicate inefficiencies in your process.
TCC smart temperature sensors
Understand the life history of your process to maintain quality production
ifm’s dual element temperature sensor, TCC, uses additional internal memory for edge processing of temperature trend data in the form of a histogram. The histogram helps determine the temperature profile over the life of the sensor. Having a “life history” of the sensor is a key tool in managing maintenance and quality assurance issues. This trending information can be extracted via IO-Link communication.
VV vibration monitoring sensors
What if your equipment could provide alarms before it fails?
Industrial-grade machine protection integrates directly into your existing control platform. Machines are continuously and permanently protected, and unlike intermittent single measurement monitoring systems, the VV simultaneously monitors equipment for the five categories of machine problems: impact, fatigue, friction, severity, and temperature. This allows timely and predictable scheduling of maintenance before major damage or failure and production downtime.
The embedded IO-Link technology provides this data in real time, giving the VV sensor the capability to predict pending failures and mitigate catastrophic damage.
MVQ smart valve sensors
Improve your process control with smart valves
In almost every production facility where fluid is flowing, valves are used to start, stop, change direction of, or control the amount of liquid or gas flow. In many of these plants, there is no feedback to tell operators and maintenance personnel the health of the valve or whether it is open or closed. Without this basic information, how can you guarantee the quality of your product? IO-Link increases insights about the status of your valves that leads to increased efficiency and decreased downtime. With IO-Link, your valve can now provide you
- Early warning to changes in how the valve moves, preventing poor production quality.
- A visual representation of the valve’s real-time position on an HMI.
- Proof that the product is being made as intended with no obstructions in the valve.
- A time and date stamp when a valve took too long to open or close, potentially preventing unplanned downtime.
OPD profile error proofing sensors
A better alternative to complex vision systems for error-proofing checks.
Assembly and error-proofing applications can be costly if not done correctly. Solutions for these applications range from single point lasers to complex camera systems requiring appropriate lighting.
The pmd Profiler projects a laser line that very accurately measures the contour of the part. At its simplest, the profiler is a point-and-shoot device that provides highly accurate pass/fail information. It is immune to extraneous light, so anyone can get up and running quickly with no prior experience.
With IO-Link
- Evaluate detailed information, including internal operating temperature and number of power cycles, for increased manufacturing efficiency and quality.
- Determine key production figures, like scrap rate by tracking the number of pass and fail inspections, to increase plant effectiveness.
DTI RFID read / write heads
Add serialization for tracking and item level process control to any project
ifm's IO-link enabled tracking solutions address every aspect of OEE (overall equipment effectiveness). With all resources in one place, it’s never been easier to identify your next continuous improvement project to boost operating efficiencies.
Tracking and Tracing solutions begin with serialization of things, and end with increases in quality, production throughput, and machine availability. Easily add tracking solutions to an open IO-link port on any master, or existing project, and realize the numerous rewards of item or workpiece serialization.
- Smart tooling
- Error proofing
- Access control
- WIP management
- ...and many more
Identification data makes it to the PLC to control your process locally, and by utilizing the IoT port on enabled masters, identification data is communicated simultaneously directly to your ERP/MES.