Case Study: Addressing cross-belt sorter failures saves $250,000+ annually
Prevent unplanned downtime due to cross-belt sorter failures
A leading retailer experienced frequent cross-belt sorter failures at multiple fulfillment centers throughout the United States. Each failure resulted in significant financial loss, especially during peak season. These incidents regularly damaged carriers and guardrails even with a wireless vibration solution. Each incident triggered hours of machine downtime and idle operators, accruing skilled labor and replacement costs.
ifm engineers first evaluated the current vibration monitoring. Then, they designed a custom solution that provided better sensor data. Finally, they used visualization and alarm notifications to warn of potential problems. This solution increased machine uptime and approximately $250,000 in cost savings per location.

Jump to:
The challenge
- Rotating assets, such as motors, gearboxes, and bearings, are the highest causes of failure
- Traditional wireless solutions fail to detect instantaneous crashes
- Cascading effects from parcel-related damage disrupt operations
- Unplanned downtime in critical process loops causes delays
- Maintenance scheduling relies on prioritization rather than real-time data
- A system is required that integrates seamlessly with existing IT architecture
The solution
- Vibration controller with edge analytics for real-time monitoring
- The VVB (vibration IO-Link sensor) is ideal for simpler applications
- Sensors to identify other factors that cause damage
- Visual solution with customized dashboards and alarm notifications
- Simplified wiring architecture through the use of a VSE (vibration edge controller) and IO-Link


- a_peak and v_RMS indicate sorter health
- a_RMS and a_peak help detect critical asset failures
- Accurate baselines can be established during normal operations
- This minimizes damage to carriers and the sorter system, reducing non-productive time (NPT)
Results
- $250,000 in annual savings (per location)
- $30,000 in savings on replacement parts by proactively addressing catastrophic failures
- Reduced operator downtime
The ifm engineers discovered that the existing wireless vibration solution was too slow to respond to sudden parcel-based impacts. And it didn't safely shut down the operation in time to avoid costly damage. Cascading damage occurred before the system warned of a potential jam.
ifm provided a system with continual crash detection and critical asset health monitoring. It uses a VSE153 vibration controller with edge analytics for real-time monitoring, and intelligent temperature sensors to identify temperature increases from excessive friction or other problems. It also has a visual solution with a customized dashboard and data historian for easy data access. It sends alarm notifications via text or email warning of changes as they occur.
The retailer invested $20,000 for a proof-of-concept solution independent of the sorter's system controls. During the trial period, the solution sent alarms minutes before a jammed parcel caused a catastrophic failure that impacted seven carrier units and cost $30,000. On average, there were more than ten similar incidents each year, with varying degrees of severity.
After scaling and integrating the solution into the controls and network infrastructure, the retailer projected more than $250,000 annual cost savings per location.
Technologies
Explore the underlying technologies that power this solution.
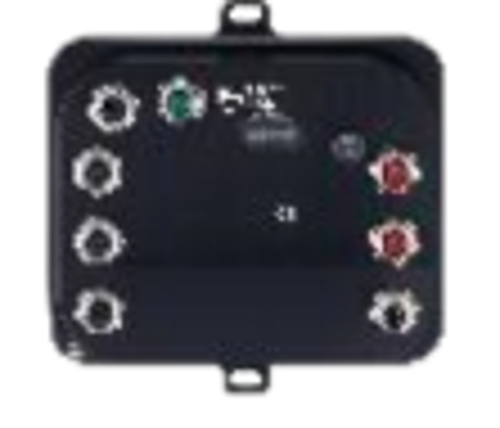
Vibration controller with edge analytics monitored the process in real-time. Because the condition was continuously monitored and evaluated, detection of early warnings of parcel jams were accurately detected and communicated.

RTDs were placed throughout the process to identify rising temperature caused by excessive friction or other effects.
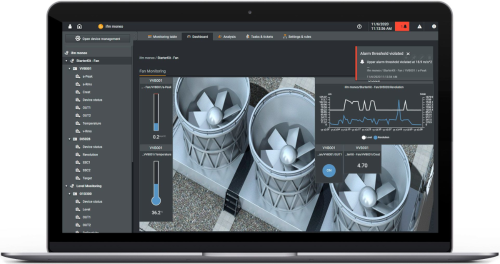
moneo|software: drag and drop dashboards to implement real-time monitoring of vibration values. These visuals can be programmed to send alarm notifications via text/email to warn of changes when they first occur.
Gain a competitive edge with ifm
To learn more about ifm sensor systems and asset reliability products to improve the performance of your complete operation contact your local ifm Sales Engineer or email cs.us@ifm.com.