- moneo IIoT platform
- Improve manufacturing processes
- Maintain process quality
Maintain process quality and product consistency in real time

Quality losses include product defects and a higher reject rate. By closely monitoring each step of the manufacturing process, deviations can be corrected in real time. moneo is an IIoT platform that logs process data, visualises trends and notifies you when your process starts to deviate.
Examples of real-time quality monitoring
- Continuous temperature monitoring of a process tank: Replace manual data logging.
- Recipe management provides consistency: Monitoring all aspects of a process ensures that the same product is produced every time.
- Conductivity measurement of fluids in a clean-in-place system: Reliably detect changes from product to cleaning chemicals to avoid cross-contamination.
Real-time monitoring of the process offers the following
Detect process deviations
Detect and monitor deviations and process drift in real time to avoid costly scrap, reworking and product recalls.
Ensure product safety
Monitor critical components using intelligent sensors and visualisation software.
Meet customer requirements
Error proofing your manufacturing processes ensures your product meets the highest quality standards to meet your customers’ expectations.
Data logging made easy –
save time and minimise errors
Manual data logging relies on human personnel, making it susceptible to errors due to fatigue, lack of attention or misunderstandings.
- Automatic data logging is conducted in real time without human intervention and allows you to assign more value-added activities to your employees.
Manual process
Process data is recorded manually and stored offline for analysis including regular trend analyses.
Automatic process
Digital process data is continuously transferred to moneo and can be accessed at any time.
Manual | Automated | |
---|---|---|
Data collection frequency | Periodically determined by the user, authority, etc. | Continuously in real time |
Required working time | Intensive: manual recording, storage, analysis, etc. | Simple: frees up employees for value-added activities |
Data accuracy | Potential errors when reading process values | Digital values, no loss of accuracy |
Data continuity | Increased risk of overlooking anomalies outside of recording time | Continuous, no risk of overlooking process deviations |
Real-time process monitoring and data logging with moneo Cloud
In many food and beverage applications, regulatory authorities require manufacturers to record certain process parameters such as pasteurisation time and temperature.
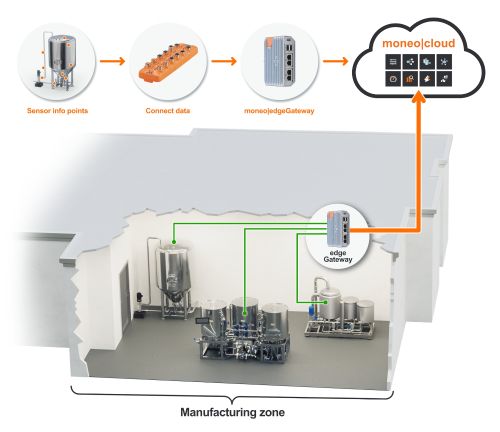
moneo – process visualisation made simple
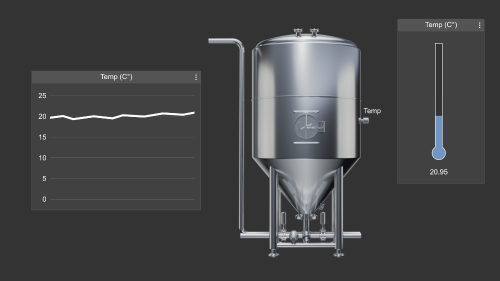
Typical components for data recording of temperature deviations
Components | Description | |
---|---|---|
![]() TCC temperature transmitters |
TCC temperature transmitter with calibration check technology
|
|
![]() IO-Link master |
Data acquisition via IO-Link for standard PLC controller or data transfer to OT/IT systems
|
|
![]() moneo edgeGateway |
Cloud connection for all IO-Link masters and vibration controllers
|