- ecomatmobile
- mobile IoT
- Predictive maintenance
Maintenance optimisation for mobile machinery
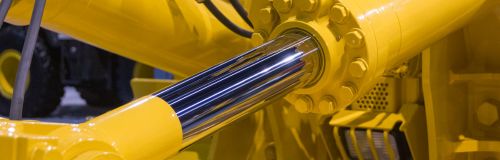
Optimise service and support times
Reduce maintenance downtime
Locate any machine anytime, anywhere – with mobile IoT. Thanks to a live connection, you can centrally display the current state of all your machines. Use remote status monitoring to determine whether a machine requires maintenance and catch problems faster. This ensures faster response times and minimises machine failures, saving you and your customers money. Instead of keeping an eye on every single machine, alarms can be installed as an alternative or in addition. Messages sent to your Technical Support will immediately inform them about problems, changes to the machine status or upcoming maintenance intervals. The switched alarm can also directly trigger a service process. This guarantees maximum uptime and helps you minimise downtime.
Demand-driven planning and preparation of maintenance activities
Service specialists have limited time and capacity, and time spent on the road is costly. Some problems are easy to solve and do not require on-site specialist support. Using mobile IoT, the existing problem can be identified by the experts in the central machine management and possibly even remedied through remote maintenance. The cost of deploying a service technician can be saved. But even if a technician is required on site, identifying the problem beforehand will give your technician a better idea of what they should be looking for and what tools and spare parts will be necessary. This information helps them accurately prepare and schedule the maintenance activity, and use the time spent on site efficiently.
Predictive maintenance: beneficial for the machine and the customer relationship
Thanks to a live connection between your machines and the cloud, you can monitor the state of all your machines. Remote status monitoring helps you identify faulty machines or specific problems at an early stage. If necessary, you can proactively provide your customer with spare parts. This minimises downtime, which in turn increases customer satisfaction. In addition, this methodology, called predictive maintenance, can maximise the service life of your equipment or machine.
Advantages and benefits of mobile IoT for service and support
mobile IoT = machine and business management and service and development tools
- Minimise downtime: mobile IoT enables users to gain quick and clear insights into the status of their machines
- Locate machines: The status and location of one or more machines can be permanently monitored
- Problem diagnosis: Machines can be checked from a distance to obtain a quick overview of any problems that have occurred
- Software and parameter updates on demand: Software, parameters or machine options can be updated or changed remotely
- Accelerate customer adoption: mobile IoT will give you a head-start by knowing about problems before the customer asks for help
- Save service costs: Receive information about required tools and spare parts before sending out a service technician to reduce service and travel costs