Determine cooling quality automatically and ensure process quality

Detect faults early and ensure optimal cooling performance
Goal of the project
The cooling of systems and machines is important for production processes.Insufficient water supply, cooling channels becoming clogged or heat exchangers becoming calcified can have a major impact on cooling performance. In the worst-case scenario, machine components overheat – ultimately resulting in plant failure.
To guarantee consistent cooling, the temperature in the feed and return lines must be monitored continuously. The IIoT platform moneo, paired with the appropriate sensors, monitors systems and automatically sends warning messages when deviations occur. When temperature deviations occur, an automatic alarm is triggered so that maintenance engineers can intervene immediately, thus preventing high follow-on costs and damage.
Prevention of delivery delays |
Assurance of |
Optimised |
On average, customers achieve: |
||
€ 160 savings per unplanned |
5 h savings by preventing |
€ 2,500 Savings in material and |
Advantages of consistent cooling performance
To ensure consistent cooling performance, the IIoT platform moneo helps by detecting temperature changes in the cooling circuit. The values recorded by sensors are processed in moneo and provide information about the condition of the respective systems. When monitoring the temperatures in the feed and return lines and the flow speeds, the Dataflow Modeler calculates the amount of heat, thereby detecting reduced cooling performance at an early stage. moneo detects leaks immediately, enabling a quick response to changes in the process. Overall, moneo safeguards the cooling circuit and displays all energy consumption transparently and visually.
Result: Monitoring cooling circuits with moneo serves not only to ensure the quality and continuity of production processes, but also to conserve valuable resources.
Value proposition
|
|
|
Ensure cooling performance: avoid calcification, blockages and leaks
Proper cooling of machines and plants is an important aspect in production. To this end, preventing lines from becoming blocked by limescale or other mineral deposits is essential. Heat exchangers becoming clogged can also be hugely detrimental to the process and result in minimised cooling performance. To calculate the amount of energy required, the requirement per piece produced must first be calculated. If this value changes, it is an indication of heat dissipation and needs to be addressed by maintenance staff.
moneo is simple and highly effective to operate. Machine and plant failures are avoided and processes are safeguarded.
moneo simulation video
Automate processes and use interfaces to SAP and the cloud
The combination of ifm hardware and software enables processes to be automated simply and effectively. ifm provides a variety of interfaces for processing and forwarding sensor values. Using different protocols, such as MQTT or OPC UA, data processed in moneo is transferred to a third-party system or directly via a specific connection to AWS, Azure or the moneo Cloud. You can store your data and carry out additional analyses in the moneo Cloud if required.
If moneo is used on-premises, the integration of ifm’s SFI (shop floor integration) interface offers a direct connection to the SAP PM module. If the temperature changes, warnings and alarms can be sent directly by email to the maintenance engineer or directly to SAP. Depending on the setting, further processing and, if necessary, automated order placement – such as a maintenance order or ordering a spare part – takes place in SAP.
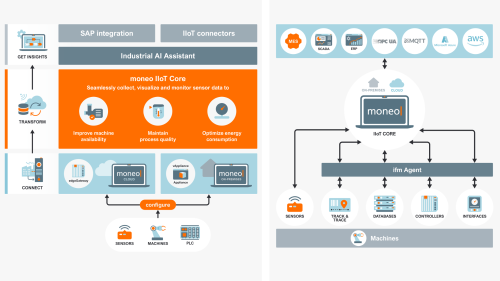
- moneo
MQTT or OPC UA →AWS, Azure, SAP - Alarm
email notification (threshold) - Spare parts
automatic ordering through SAP - Cloud and on-premises
possible with the cloud and on-premises solutions
Cooling circuit management: how to monitor coolant in a targeted way
To monitor your cooling circuit with moneo, the software is either installed on a server (on-premises or in a virtual environment) or you can use the application directly in the moneo Cloud. An IO-Link master is connected to the internal network (VLAN). First, the heat quantity is calculated from the flow values of the temperature in the feed and return lines. By calculating the amount of heat, conclusions can be drawn about the cooling process.
moneo converts the recorded sensor values into process-relevant information and provides detailed information about cooling water consumption. All sensors in the process are clearly visualised in moneo via dashboards. Deviations are displayed in real time and the need for action is identified at an early stage. The comprehensive monitoring of the process and the associated identification of exceeding and falling below threshold values enables a quick response to changing parameters through integrated alarm management.
Conclusion: Monitoring cooling circuits ensures process quality This ensures optimised plant capacity utilisation, and unplanned failures no longer occur. High energy costs are also reduced and the heat generated can be used in other processes.

System structure
- IO-Link master (VLAN)
- Power supply
- Cooling water control panel
moneo software
- Historical data
- Visualisation
- Monitoring
- Alarm function
- Threshold violations via SFI to SAP