Increased efficiency in metal panels handling results in savings of 50%
The OPD100 helps to save material handling costs in the five-digit range at German automotive manufacturing plant
Resistant to extraneous
light up to 20,000 lux
Flexible, distance-independent
object positioning
Quick set-up
No expert knowledge needed
Results
- The PMD Profiler reliably detects two panels placed upon one another
- Reduced transport routes and storage costs
- Resistant to extraneous light and easy to position
- Easy set-up in just a few minutes; no expert knowledge needed
The challenge
In the BIW assembly lines of automotive manufacturing plants, high material handling costs arise during production due to the supply of semi-finished products from the stamping facility to the production line. For example, approx. 4000 door panel components per day need to be transported by truck.
The capacities of the trucks and the load carriers used to transport the doors have an influence on the number of required transport routes and thus directly on the logistics costs. Moreover, free space in the vicinity of the production lines is required for parts that need to be stored before being fed into the production line.
This is why the capacity of each load carrier offers great potential to keep logistics overheads and storage space to a minimum. The aim was to reduce material handling costs while at the same time maintaining production quality. The idea was to have the load carrier transport twice as many door panel components. This saves 50% in material handling costs and also 50% in storage costs (required space). However, as the robot was not capable of safely unloading each panel piece by piece from the load carrier, this needed to be ensured by means of an additional sensor system.
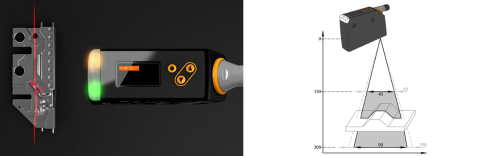
The solution – why ifm?
This is where the OPD100 came into play. With only a few pushes of a button, the sensor was set up quickly, and safely detected when two panels instead of one had been placed upon one another.
Thanks to the profile sensor (OPD100), we have closed the gap between the rather simple and low-priced distance sensors and the complex and sometimes very costly vision systems. The profile sensor is a true all-rounder and offers a solution for many quality control and position detection applications.
We are able to provide our customers with a very robust solution that also works reliably under extraneous light and with differently coloured objects. Objects can be very flexibly positioned within the laser line, and the special thing is that the sensor can be set up within minutes without additional software thanks to its three push buttons.
After having been successfully tested in one facility, this application immediately was added to further production systems. So all in all, a small investment has resulted in an improvement and in the saving of costs.