How you can safeguard your processes with digital data acquisition

Unearth your treasure trove of data and ensure process quality
Goal of the project
An abundance of data is generated in a production process: temperature values, fill levels, piece counts, water consumption, power consumption and much more. Would it not make sense to put this potential to good use and generate major added value for your company? Your data contains all the information you need to ensure your processes and quality. We will work with you to unlock this potential. Instead of you spending a long time and covering long distances in production to manually record the data, sensors can record the respective values directly on the machine and do so precisely to the second.
As a full-service provider, ifm provides both the hardware and software to record and analyse your data – everything from a single source and with the expertise and experience of over five decades. From the very beginning, you can safeguard your processes effortlessly and efficiently, use your resources perfectly and therefore considerably cut costs.
By the way: you can also use moneo with your existing sensors.
Transparency of |
Identification of |
Quality assurance |
On average, customers achieve: |
||
100% Fewer routes |
€ 2,950 Savings in personnel costs |
100% ROI after |
Ensure process quality
- Aim of the project
- Advantages of digital data acquisition
- Data acquisition made easy: digital processes instead of manual data entry
- Collect production data and evaluate it with moneo
- Data acquisition and data transfer: interfaces to SAP or the cloud
- How to integrate digital data acquisition into your processes
Advantages of digital data acquisition
Digital production offers numerous advantages. Whereas previously an employee had to manually record data on the various machines, sensor technology can now be used. The perfectly tailored software solutions from the IIoT platform moneo offer numerous options for subsequently processing the data and visualising entire processes.
The result:
- Pinpoint data acquisition
- Sensor technology instead of manual data acquisition
- Process transparency
- Rapid response capability to changes in the process
- Assurance of process and product quality
- Improved employee capacity by eliminating long inspection routes
Conclusion: overall, the entire organisation is improved, which saves a lot of time and resources and makes the entire process efficient and transparent.
Value proposition
|
|
|
|
|
|
Manual process
Process data is recorded manually and stored offline for analysis including regular trend analyses.
Automatic process
Digital process data is continuously transferred to moneo and can be accessed at any time.
Data acquisition made easy: digital processes instead of manual data entry
Automated data acquisition precisely records the values down to the second, thereby eliminating lengthy manual processes and sources of human error. For transparent data acquisition, it is important to use the appropriate sensors. Depending on the application, different types of sensors are used. These include temperature, level, compressed air, power or water consumption sensors. The collected sensor values are forwarded to moneo via an interface and converted into process-relevant information using data modelling. A detailed visualisation of these values is then created, which provides an overview of the consumption of the various media.
Exceeding or falling below the process values triggers corresponding warnings or alarms. Fast response to changing process parameters through integrated alarm management is possible and damage to the machine or product is avoided by detecting it in good time. The values also show where action is required on certain points or machines in the process.
The result: the process and with it the product quality, as well as optimal deployment of personnel, are guaranteed, resources are conserved, costs are saved and plant capacity is optimally utilised.
moneo simulation video
Collect production data and evaluate it with moneo
For process assurance, automatic recording and processing of the data generated in production is essential. Important components that provide information about the process or the machine or system include:
Different sensors are used depending on the application.
Challenge: Temperature hotspots affecting converters or controls in control cabinets. If these components or machine parts continue to operate at excessively high temperatures, their service life is shortened. This can lead to malfunctions – or, in the worst case, plant failure. A thermal imaging camera is often used to check the components, which in turn requires a lot of personnel and documentation and only provides a snapshot.
The solution: A temperature sensor is mounted at the hotspots in the control cabinet. The IIoT platform moneo processes the data and provides information about the condition of the component or plant. The temperature and even the humidity in the control cabinet are automatically recorded and documented. If any deviations occur, warnings and alarms are triggered, enabling a quick response to changes in the process.
Conclusion: Additional monitoring of the temperatures in the control cabinet ensures trouble-free running of the production process and machine availability. This allows future failures to be identified and remedied at an early stage.
Challenge: Level sensors are used to measure the fill level of tanks or barrels, for example. Without a suitable solution that automatically records the data, an employee has to go to the system every two days, read the fill level on the sensors manually and enter it in a list.
Solution: With the IIoT platform moneo, this process is completely automated and manual entries and sources of human error are avoided. The data is recorded using level sensors and if the level falls short, an automatic message is sent to the maintenance engineer via email or via the SAP PM module.
Conclusion: Real-time level monitoring registers changes immediately, enabling a quick response. An automated ordering process can also be introduced for replenishing raw materials.
Challenge: In many industrial sectors, consumption is already recorded – but often still manually. There is a lack of central evaluation of individual consumption, peak consumption and total consumption. Unwanted consumption also occurs outside of operating hours and cannot be identified. This means that there is no way to identify cost drivers in energy consumption.
The solution: To record electricity consumption, energy measuring devices or electricity meters are installed in the system. Manual processes to record consumption per week or month, irregular reading cycles, or even transposed digits when documenting by hand are eliminated. By digitally recording electrical energy consumption and then processing it with moneo, all savings and optimisation measures can be documented. The resulting energy transparency lastingly increases awareness of energy consumption (total and peak consumption, consumption in standby and during non-production times, reactive currents and reactive power), thus ensuring a more resource-saving use of electricity.
Conclusion: With moneo, data is recorded automatically and precisely to the second. The data evaluated is transparent and can be seen at a glance. This will help you identify savings opportunities.
Challenge: In companies, consumption is often recorded manually. For the assessment, optimisation and cost reduction of total energy consumption, automatic recording of consumption is necessary. This includes visualising and analysing all consumption, combining several meters into one total meter, identifying energy cost drivers and peak consumption, and recording consumption outside of operating hours.
The solution: With moneo, you can use flow sensors to automatically record your water consumption down to the second and obtain an overview of your processes. This eliminates sources of human error, time differences in data collection and irregularities. You also save time that you can use for other tasks.
Conclusion: Integrating flow sensors and the IIoT platform moneo for consumption recording enables a clear overview of energy consumption. Devices or processes that consume excessive amounts of energy are detected and visualised. The transparent mapping of the processes also makes planning decisions easier.
Challenge: Machine tools feature general display instruments to show their various operating states. However, the process data of the compressed air consumption in combination with the associated costs is not monitored. This means that an assessment within the framework of energy management and energy efficiency measures cannot be made. To move away from manual processes and resulting sources of errors such as transposed digits and irregular cycles, automating processes efficiently is essential.
The solution: By using compressed air meters and the IIoT platform moneo, data can be recorded on the machine tool itself – and here, for example, also on the compressed air gun in this company. The goal is to ensure energy-efficient operation of the machine tool. This requires calculating different compressed air costs to assess and organise energy-saving measures.
Conclusion: Overall, the energy and operating costs are reduced with the aim of becoming a “green” factory. Unnecessary costs in standby mode due to leaks are identified at an early stage and clearly visualised.
Challenge: A large number of products and components are manufactured daily at a production plant. The quality of the individual components must be simultaneously monitored and checked so that no defective parts are produced – with the associated high waste of resources – and failures in the production process do not occur.
The solution: Recording data with the appropriate sensor (piece counter) and processing it using the functions of the IIoT platform moneo makes it possible to monitor the production process and carry out quantity-based maintenance, thereby ensuring process quality.
Conclusion: Overall, quantity-based maintenance promotes transparency in the production process and ensures the quality of the products manufactured.
Data acquisition and data transfer: interfaces to SAP or the cloud
Data acquisition using appropriate sensor technology and evaluation in moneo is an important step towards digitalised production. If you want to take it a step further, you can make additional use of the processed data by forwarding it to the cloud or SAP. This requires appropriate interfaces, which ifm can provide you with. The data processed by moneo can, for example, be forwarded via various protocols using MQTT or OPC UA. This allows direct transmission to AWS, Azure or SAP. Depending on the customer’s wishes, in the event of an alarm message, it is also possible to automatically place an order or trigger a required maintenance order in the SAP PM maintenance module. In addition to AWS and AZURE, moneo can also be used directly in the moneo Cloud.
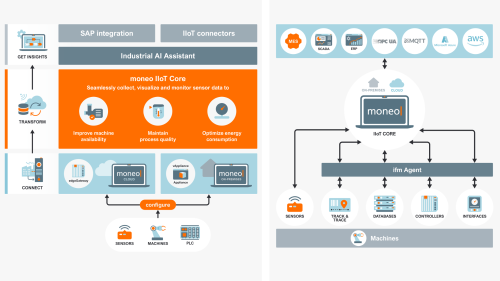
- moneo
MQTT or OPC UA →AWS, Azure, SAP - SAP Integration
SFI (shop floor integration) →SAP PM - Alarm
email notification (threshold) - Spare parts
automatic ordering through SAP - Cloud and on-premises
possible with the cloud and on-premises solutions
How to integrate digital data acquisition into your processes
Would you like to take advantage of the benefits of digital, automatic data acquisition, thereby perfectly aligning your process and ensuring your product quality? We will support you in finding the most suitable sensors and software solution for you and integrating them into your system. Firstly, the corresponding sensors are installed in the respective plant, or existing sensors are used. If you already have sensors but do not have the appropriate tool to fully evaluate the data, we will check the compatibility of your sensors with moneo. moneo is then installed centrally on your server or, if you would prefer, a direct connection is established to the moneo Cloud. In moneo, a digital twin of your plant is created and the threshold values are set.
You can now easily and quickly monitor your process, ensure your product quality and make your consumption transparent.