Water consumption, leaks and cooling performance

Determine water consumption, avoid leaks and thereby ensure cooling performance
Goal of the project
A reliable cooling water supply is essential for cooling machines and plants – regardless of the production environment. Reduced cooling capacity caused, for example, by insufficient water supply will greatly increase energy costs and, in the worst case, result in overheating of machine components and ultimately in plant failure. Leaks are a common cause of reduced cooling performance. Leaks allow fluid to escape – often unnoticed at first – and the volume of cooling water required decreases and the temperature of the remaining fluid consequently increases. If the temperature increase is not detected or is detected too late, high costs arise due to overheating of the motor, which can lead to complete plant failure.
To ensure process quality, monitoring the cooling water volume and temperature and detecting any leaks at an early stage is, therefore, essential. Monitoring is carried out via sensors that collect measured values in real time. The intelligent and easy-to-use IIoT platform moneo evaluates this data and provides immediate feedback when values exceed or fall below the threshold level. In this way, using simple means enables you to avoid plant failures due to overheating and the high consequent costs.
Plant |
Identification of |
Setup possible |
On average, customers achieve: |
||
€ 80 savings per unplanned |
€ 500 savings due to cleaning |
100% transparency |
Optimise energy consumption
- Aim of the project
- Safeguard production capacity and conserve resources by monitoring cooling circuits
- How early-stage detection of leaks works
- Monitor cooling water volume with the help of AI
- Use monitoring data in other systems
- How to monitor your water consumption, avoid leaks and ensure consistent cooling
Safeguard production capacity and conserve resources by monitoring cooling circuits
The advantages of monitoring cooling circuits with the moneo software solution are obvious: Rapid detection of even minimal leaks, combined with a quick response, prevents the far-reaching consequences of fluid loss. The manufacturing process and, ultimately, the product quality remain assured while all key indicators are simultaneously and transparently visualised in moneo. Energy consumption does not increase uncontrollably because no additional energy has to be used to compensate for the falling water pressure. A valuable resource, water, is also conserved because only the absolutely necessary amount is used in the cooling process.
Result: Monitoring water consumption and the associated cooling circuits using moneo results in energy being used optimally and ensures trouble-free production processes and a considerable reduction in costs.
Value proposition
|
|
|
How early-stage detection of leaks works
In various areas of production, coolants such as water or water-based cooling media protect machines and plants or keep them at the desired operating temperature. However, if a leak occurs somewhere, fluid will escape from the cooling circuit in an uncontrolled manner. The escaping coolant can damage machines, fixtures, components, etc. in the production line and represents a hazard for personnel – e.g., the risk of slipping. If too much cooling water escapes, the cooling circuit may even switch off completely because the pump can no longer maintain the pressure in the system. Detecting any leaks early on, before litres of coolant have already leaked out, is essential.
In this context, the interaction of sensors and the IIoT platform moneo makes it possible to monitor the volume of coolant in general and the use of energy in particular. To do this, the machine temperature and the amount of coolant are constantly monitored. This allows leaks that do not occur directly at a measuring point also to be recorded, as well as damage to hoses and caps. Depending on the application, a complete production facility with 20 machines connected to a cooling circuit can be monitored through simple installation and commissioning of just two sensors. As soon as a leak occurs in just one machine, it is detected and an automatic message is generated.
By the way: you can use the heat generated in the production process to heat company buildings. This allows you to make optimal use of the energy and simultaneously reduce your overall energy costs.
moneo simulation video
Monitor cooling water volume with the help of AI
Artificial intelligence facilitates dynamic monitoring of complex machine and production processes. To monitor the coolant, critical process variables in the process, such as the flow, must be observed. The flow in the feed and return lines of a cooling circuit provides information about flow fluctuations and, therefore, about plant condition.
The AI-powered assistant moneo PatternMonitor monitors critical process values and sends alarms at an early stage in the event of deviations from the normal state. This allows trends, changes in levels and fluctuations in volatility to be identified. If the module detects a significant level change in the process values, this may indicate a leak in the system. Thanks to the integrated alarm system, immediate action can be taken to locate and resolve the problem, such as an inspection of critical areas in the production line.
The moneo tool is simple and intuitive to operate, so no data science expertise is necessary.
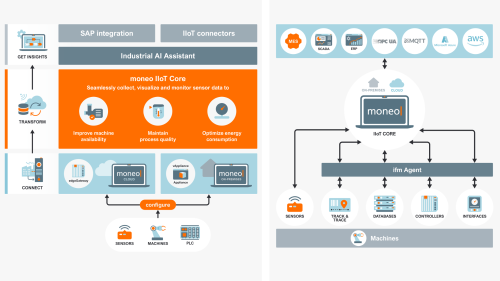
- moneo
MQTT or OPC UA →AWS, Azure, SAP - SAP Integration
SFI (shop floor integration) →SAP PM - Alarm
email notification (threshold) - Spare parts
automatic ordering through SAP - Cloud and on-premises
possible with the cloud and on-premises solutions
Use monitoring data in other systems
The IIoT platform moneo offers numerous options to protect machines and plants from leaks, for example, thereby ensuring continuously consistent process quality.
The data prepared in moneo can be exported via different protocols such as MQTT or OPC UA for using in third-party systems such as AWS, Azure or SAP. moneo offers a direct connection to SAP PM by integrating ifm’s own SFI (shop floor integration) interface.
The interface offers the possibility of automatically triggering corresponding follow-up processes in the event of warning messages – from ordering spare parts to creating maintenance orders. moneo is also compatible with existing sensors, making it even simpler to integrate it into your existing systems. Monitoring using artificial intelligence means that deviations and fluid loss can be detected at an early stage.
Even small leaks that do not occur directly at the sensor are detected. The use of artificial intelligence is currently available with the on-premises licence. In the future, all AI solutions will also be available in the moneo Cloud.

System structure
- Power supply
- IO-Link master
- Magnetic-inductive flow meter
moneo software
- Historical data
- Visualisation
- Monitoring
- Alarm function
- Threshold violations via SFI to SAP
How to monitor your water consumption, avoid leaks and ensure consistent cooling
The moneo software allows you to monitor your cooling circuit either by installing it on a server (locally or in a virtual environment) or by using it directly in the moneo Cloud. An IO-Link master is connected to the internal network (VLAN). Two flow meters are installed in the feed and return lines of the cooling circuit and are used to monitor the amount of cooling water required.
The AI-based PatternMonitor has a built-in function that automatically detects leaks. The difference between the flow values of the feed and return lines should theoretically be exactly zero. In practice, this value fluctuates strongly around zero, and significant outliers occasionally occur. Monitoring with static threshold values is therefore not ideal because the threshold value would have to be set quite high and with a response time.
The PatternMonitor module monitors a process value with the aid of statistical methods. This allows trends, level changes and fluctuations in volatility to be identified. If the module detects a level change in a time series, this indicates a potential leak in the system. The integrated alarm system makes it possible to take further measures, such as checking critical points in production, to resolve problems.
Conclusion: The required energy is used optimally and unnecessary costs are avoided. At the same time, the running process continues and unplanned downtimes are avoided.