- 3D object recognition
- Pallet Detection System (PDS)
- Software design
Software design
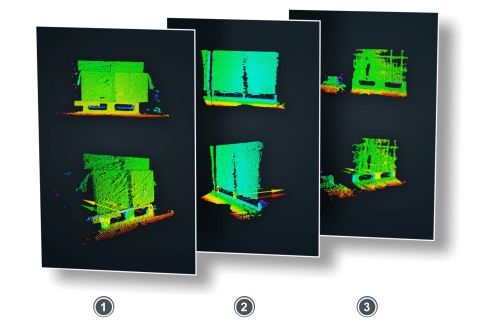
Even in adverse environmental conditions, the sophisticated software solution will lead the lift fork reliably to its destination by means of the 3D point cloud of the ToF camera.
The development of the software was based on the collection and use of real-world data. This approach reveals all of the challenges faced by vehicles operating in the "messy" material handling industry. The PDS has to detect damaged pallets as well as pockets covered by shrink film; besides, there are many other imperfections which may lead to faulty pallet detection.
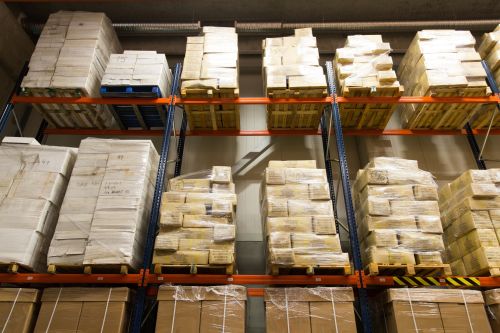
The PDS can detect different pallet types as well as more than 400 special cases which may occur in real working conditions. The number of scenarios the software can reliably solve is continually growing, making sure that the PDS solution will work reliably in all environments, even in harsh conditions.
The PDS software process
Generate a full 3 dimensional point cloud
In a first step, the PDS pallet detection processes the amplitude and distance data detected by the O3D3xx vision sensor. These images can contain interference and artefacts due to harsh environmental conditions.
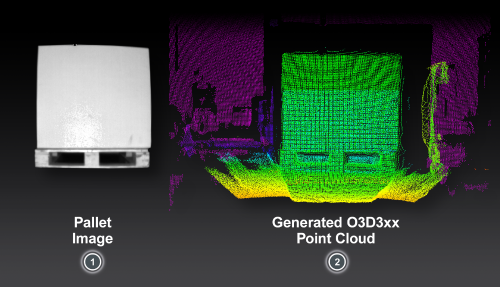
Filter the image
In the next step, the image is filtered and unwanted pixels are removed. This is a critical step for reliable pallet detection.
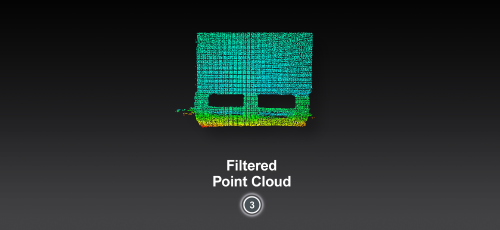
Determine the six degrees of freedom
The filtered image is then used to exactly determine the location and position of the pallet and its pockets in three dimensions.
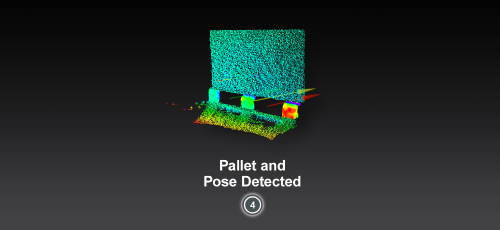
Using this approach, the following PDS specifications were achieved:
- Designed for all standard pallets with two pallet pockets
- Ranges up to 2m (4m when using corresponding HW)
- Position accuracy of +/- 1cm
- Detection time of <1 second
- Communication via Ethernet or CAN