- Profiler
- Applications
Applications
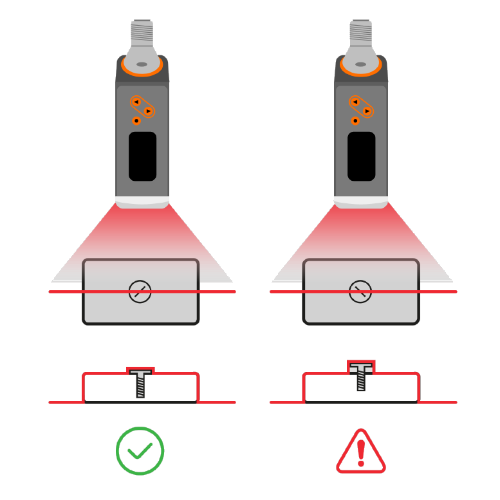
The pmd Profiler is ideal for determining very small differences between parts. Below are just a few example applications.
Assembly of welded parts
Ensuring parts are in the correct positon prior to welding typically requires vision systems.
The pmd Profiler provides a precise laser line and shows even the slightest misalignment of parts.
- No challenges due to external light
- Highly accurate analysis across the entire part
- Simple Pass/Fail output with easy setup allows for quick installation
Sorting and orientation
Monitoring whether the correct metal ring has been mounted in an upright position
The PMD Profiler is applied in, for example, the automotive industry, where there are hardly any differences between a correctly and incorrectly selected ring. It creates a profile of the two parts and gives a matching value between the reference and the present object. If this value falls below a freely selectable threshold value (for example 85%), a bad part is identified as such and can be sorted out.
In this application, there is only a small difference in height, which pushes 1D sensors to their limits. Even with camera systems the application cannot be solved easily because of the low contrast which is further deteriorated by ambient light. Accordingly, expensive external lighting sources would be needed, which can be omitted with the PMD Profiler. With the PMD Profiler, only one device is needed to check whether the right part is present and has the right orientation. Also, with the use of the PMD Profiler's patented system with two green markers on the red laser line, a Region of Interest (ROI) can be set in order to focus the sensor's examination onto the relevant area, i.e. the rising of the rings on the edges.
In any assembly operation the orientation of parts is critical. This is true for a variety of industries such as automotive, medical and packaging. The pmd Profiler is checking if the orientation is correct prior to performing another task. If this is not done correctly then the machine crashes and production stops.
- Robust on shiny parts like rotary bearings
- Detailed profile measurement can determine orientation in the medical industry
- Optimize the performance of a packaging machine by quickly discarding parts with the wrong orientation
Fill level
Traditional optical sensors perform differently when trying to sense different target materials. The pmd Profiler can easily detect both the food product and the packaging. A quick check of the fill level is easy to determine.
- Robust measurement on targets with different materials
- High accuracy results to meet the demands of the packaged consumer goods market
Control of correct machining
Distinguishing the gear contour of an unprocessed and a machined component
In this application, the task is to recognise whether a component has already been processed, i.e., whether the gear contour is already present or whether there is still a flat surface. While such an application can virtually not to be solved with a 1D sensor, the PMD Profiler reliably detects the profile of the components and detects changes in the contour with very high precision. In the case of a solution with a camera system, the differences in contrast would have to be emphasised by shielding and external illumination, which would cause additional expenditure and costs.
Gap control
Checking the latching of an interconnected clamping system
The PMD Profiler checks whether a clamp is latched completely. This way, gaps indicating insufficient latching can be detected in order to prevent scrap or, if undetected, failures at the customer. Here, the ROI can help to increase the difference between a good and a bad part's matching value so that these parts can clearly be distinguished.
Depth measurement
Checking the tightening of a screw
In this application, the correct tightening of a screw needs to be monitored. This is virtually impossible with a 1D system as its light spot can only focus on one of the two positions, i.e. completely versus partly tightened. With camera systems, the installation effort would be extensive compared to the PMD Profiler's quick set-up despite the same precision. By means of this precise depth measurement, the PMD Profiler can be applied in a variety of applications, like for example the detection of laser labelling or the fraying of conveyor belts.