Control cabinet monitoring protecting and monitoring components
An industrial environment with no control cabinets is barely imaginable. They perform a wide variety of functions: They are used as a space for mounting components to protect them against dirt, dust and moisture. They also provide heat dissipation, EMC shielding and contact protection.
Enclosing the components in a control cabinet protects them against external influences that could lead to damage or a failure.
The starting position
If there is no monitoring of the control cabinet in terms of temperature, humidity and power supply load, operational failures may occur. In the absence of visualisation of live data, there will furthermore be no way to draw conclusions about the operating status. As a result, malfunctions will be detected late or not until a machine stoppage occurs. There will also be no optimisation of heat management or energy consumption or cooling.
Goal of the project
Status-oriented and preventive maintenance based on actual requirement
To ensure smooth functioning of a control cabinet, monitoring of the following variables is available
using ifm sensor systems and moneo. To find out how this is implemented, continue reading.
1. Monitoring of humidity and temperature
The relative humidity is a crucial factor within the control cabinet. Moisture can get into the control cabinet due to precipitation, moisture from the environment and other causes and damage components. By continuously monitoring the relative humidity in the control cabinet, this can be detected promptly and consequential damage such as corrosion or short circuit can be prevented. The aim should be to achieve a relative humidity between 20% and 60%.
The temperature is also an important factor. A maximum internal temperature of 35°C is considered ideal. A higher temperature will adversely affect the service life of the components, while a lower temperature is not efficient and will result in higher costs since more cooling capacity will be required.
Implementation
To enable monitoring, moneo is installed on a central server and the moneo RTM module is activated.
An ifm IO-Link multisensor type LDH292 is installed for monitoring to measure the temperature and relative humidity inside and outside of the control cabinet. This makes it possible to take ambient temperature effects into account. Both sensors are connected via an IoT IO-Link master (e.g. AL1350 or AL1950). The data is transferred to the central moneo RTM module via the IoT port of the master once a second.
In addition to the temperature, the LDH292 sensor also monitors the relative humidity as a process value and outputs it as a percent.
The thresholds for this application are defined according to the data sheets of the devices installed in the control cabinet.
System overview
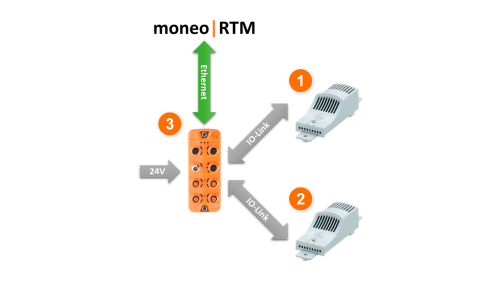
- Temperature and relative humidity sensor inside the control cabinet (LDH292)
- Temperature and relative humidity sensor outside the control cabinet (LDH292)
- IO-Link master (e.g. AL1350)
Dashboard

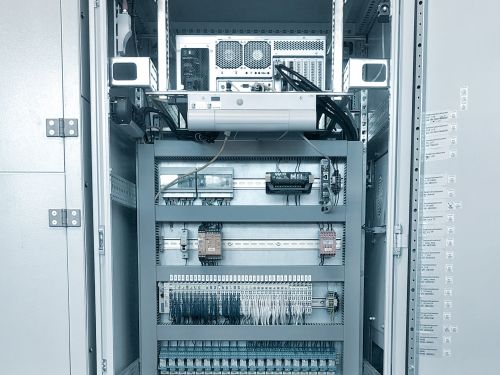
2. Temperature monitoring of hotspots
Despite the measurement of the control cabinet temperature, there may be hotspots within the control cabinet where high temperatures occur in certain areas. Typically they occur on power electronics such as frequency converters, servo drives or transformers.
These hotspots on individual components have a direct adverse effect on the service life of these components. The high temperatures can cause electrolytic capacitors to dry out faster, for example, thereby leading to a failure of the entire plant.
These hotspots cannot always be avoided by structural changes or active cooling. Because of this, it is a good idea to record the temperature directly on the component and to record operating hours depending on the temperature. This makes it possible to replace or maintain the component preventively before a failure occurs.
Implementation
moneo is installed on a central server and the moneo RTM module is activated.
To monitor the control cabinet, an ifm IO-Link multisensor type LDH292 is installed inside the control cabinet to measure the relative humidity and temperature. An additional bolt-on temperature sensor (TS2229) is installed directly on the transformer to monitor the temperature. The analogue temperature signal is converted to an IO-Link signal by a control monitor (TP3231).
Both sensors are connected via an IO-Link master (AL1350). The data is transferred to the central moneo RTM module via the IoT port of the master once a second. The temperature sensor is also coupled directly to an hour meter. It counts the operating hours depending on the temperature: The clocking moves faster at higher temperatures and slower at lower temperatures.
System overview
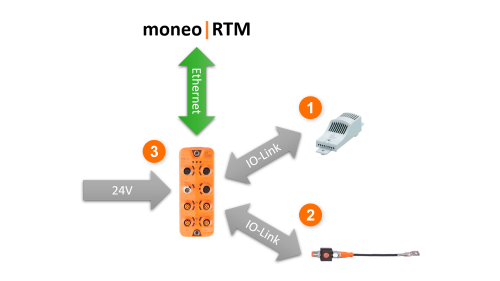
- Temperature and relative humidity sensor (LDH292)
- Control monitor (TP3231) + bolt-on sensor (TS2229)
- IO-Link master (e.g. AL1350)
Dashboard

3. Monitoring of the 24V supply
For control cabinets in general, and especially for control cabinets used in outdoor applications, special attention should be paid to monitoring of the power supply. 24V supplies are usually neglected in monitoring. These circuits are protected by simple safety fuses or are not protected at all.
Without fuse protection there is a danger of power supply overload, which in the worst case could lead to a fire in the control cabinet.
Implementation
To monitor the 24V supply, electronic fuses with IO-Link are installed, They consists of a feed module (DF2101) and the fuse modules (e.g. DF2212 with nominal current 2A). Up to eight fuse modules can be connected in series to a feed module, with each feed module consisting of two channels. This makes it possible to monitor and protect 16 circuits with a total current of 40A.
IO-Link communication continuously transfers current information about the fuse modules including:
- Current nominal current
- Output voltage
- Current device status: Short circuit, overload, undervoltage
The feed modules are connected via an IoT IO-Link master (e.g. AL1350 or AL1950). The data is transferred to the moneo RTM module via the IoT port of the master once a second.
When a channel of the fuse module is triggered, this information is transmitted by means of the device status. This status can then be generated by moneo RTM and a message can be generated automatically. This message can inform department managers that the fuse has been tripped by various means including e-mail.
The current status is also indicated directly on the respective fuse module by a button with a status LED (green = operation with no problems, red = fuse tripped by short circuit or overload). This provides support in troubleshooting and indicates directly which channel is affected. The fuse can be turned on again directly with the button.
System overview

- Feed module and electronic fuse (DF2101 + e.g. DF2212)
- IO-Link master (e.g. AL1350)
Dashboard
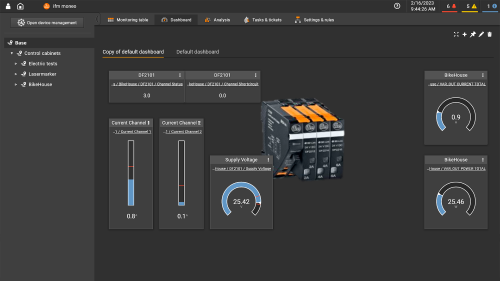
Success
Monitoring of control cabinets with a sensor system and moneo RTM thus offers many advantages in various applications:
- Errors can be promptly detected and indicated by alarms.
- Energy costs can be reduced due to optimised cooling and heating and the service life of the components in the control cabinet is extended by an optimum ambient temperature.
- Damage and unplanned down times due to moisture and temperature fluctuations in the control cabinet are prevented. Continuous power monitoring is ensured.