Condition monitoring of a fan based on the current consumption
The central exhaust system of a production hall has several fans. The fan power is decisive for the quality of the exhaust process in the entire production hall.
Exhaust air systems are required for various production processes. They are used to exhaust soldering vapours and vapours from the laser marker, and to ensure machine availability and thus the smooth operation of the entire production process. Needs-based maintenance is therefore essential.
In order to realise this, the current values of all three phases are detected on one of the fans, in addition to the already integrated vibration monitoring. Measuring the phase difference provides additional information about the condition of the fan motor.
The starting position
A compressor failure in this plant has far-reaching consequences:
- Machine downtimes as the waste heat is not sufficiently dissipated
- Costs due to the loss of production
- Possibly high repair costs
- Health risks for production personnel as soldering vapours are not exhausted
- Quality problems with laser marking as fine dusts are not adequately exhausted
In the worst case, this leads to a total failure of the entire production area.
The vibration monitoring of the fan and its data sent to moneo provide information to detect possible damage.
But additional data on the electrical condition of the fan and the upstream frequency converter are necessary for a comprehensive assessment.
Goal of the project
Extended condition monitoring of the fan by measuring the phase difference
The aim is to ensure the fan’s operability by monitoring:
- the motor windings
- the free movement of the rotating components
- the electronics in the frequency converter
Implementation
moneo RTM is centrally installed on a server. The IO-Link masters are connected to the server via an internal VLAN.
ifm has a wide range of automation components. Three ZJF056 current converters and the AL2605 IO-Link input/output module were chosen for this application.
The current converters are used for all supply lines of the three AC phases U/V/W between the frequency converter and the connection terminals on the fan. The measured values of the converters are available as 4...20 mA analogue signals on the signal outputs. These values are converted from 4...20 mA to IO-Link signals via the AL2605.
The data is made available to moneo RTM via an IO-Link master of the AL1352 series.
The values of the current consumption of the three supply lines U/V/W are to be measured with the help of three current converters.
To obtain useful process values, the measured value of the current converter must be converted into the actual current value (4 mA ≙ 0 A, 20 mA ≙ 50 A*) of the converter. This is done in moneo RTM via the function “Calculated values”.
The following electrical and mechanical damage patterns can be detected:
- Short circuits on the motor winding
- Sluggishness of rotating components
- Fault in the frequency converter
The determined current values are used to
- calculate the difference of the three phases
- determine the average current of all three phases
- compare the values with each other
* Factory setting of the ZJF056 = 100 A. To increase the measuring accuracy, the measuring range was adjusted to 50 A via the DIP switch on the converter.
Success
Process optimisation from time-based to condition-based maintenance
Thanks to comprehensive data recording, imminent faults can be detected at an early stage. Maintenance work can thus be scheduled and carried out as needed. This adds a decisive factor to the process reliability of the entire plant.
Current values allow conclusions to be drawn about possible short circuits on the motor winding, sluggishness of rotating components and faults in the frequency converter.
System structure
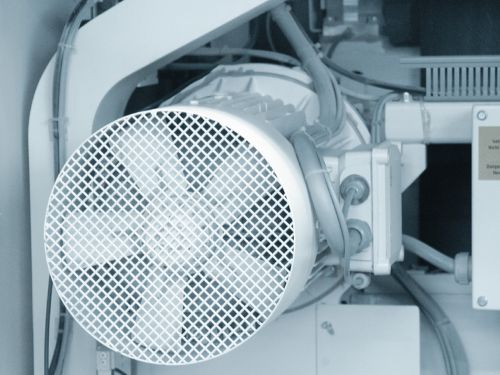
Dashboard
Get the big picture on the moneo dashboard.
The dashboard provides the user with an overview of the relevant process values for this plant.
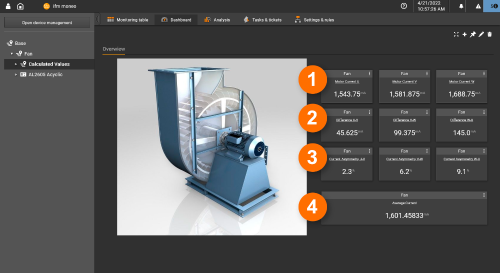
- Current value measured in mA
U | V | W - Phase difference
U-V | V-W | W-U - Current asymmetry
U-V | V-W | W-U - Average current of all three phases
Analysis
The analysis function can be used to access historical data and compare different process values. The diagram shows the current values of U, V and W in mA.
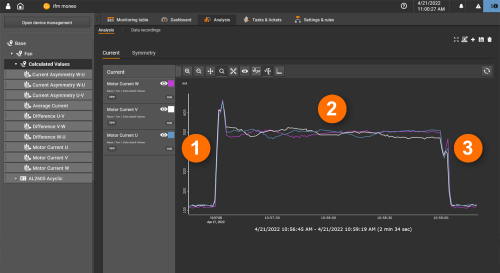
Here it can be clearly seen that in the start-up phase
- there is an overshoot, while in normal operation
- the current value settles. In the switch-off moment
- there is a small peak due to the inductances in the motor.
Settings & rules: Manage thresholds
The so-called current asymmetry should not exceed 10% for three-phase machines. For each difference value, an alarm is created if the value is ≥10%.
- Alarm when exceeding 10% deviation from U-V
- Alarm when exceeding 10% deviation from V-W
- Alarm when exceeding 10% deviation from W-V
Monitoring with regard to a warning limit value has not been implemented as the tolerance band of up to 10% may be used when the fan motor starts up or sudden load changes occur.
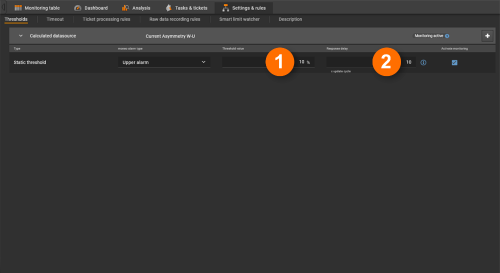
- Upper alarm threshold
- Delay time for the alarm threshold
Ticket processing rules
This function can be used to easily define what should happen after a warning or alarm has been triggered, e.g.:
- Email notification
- SAP integration
For applications where maintenance measures are necessary, it is advisable to plan the service call in good time.
Calculated values
The “Calculated values” function is used to further process the process data. In this use case, various further processing operations are carried out:
- Conversion of analogue 4...20 mA into the current value of the current converter to calculate the motor current
- Calculation of the phase difference
- Calculation of the average current of the three phases
- Calculation of the current asymmetry
In this use case, all 3 phases of the drive motor are monitored, which means that the calculation sometimes has to be carried out several times.
Conversion of analogue 4...20 mA into the current value of the current converter to calculate the motor current
The current converter used provides an analogue signal of 4..20 mA which first must be converted into a process value in mA. This must be done for all 3 phases.
Motor current = (AIN-4,000) * ((AEP-ASP)/(16,000)) + ASP
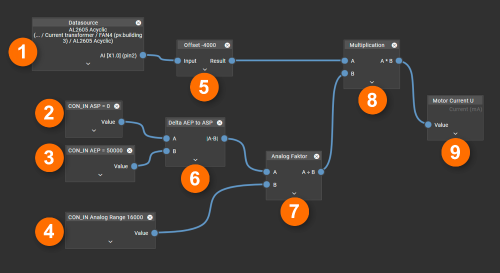
- Analogue current value of the current converter (4...20 mA)
- Constant: Analogue start point (0 mA = 4 mA)
- Constant: Analogue end point (50,000 mA = 20 mA)
- Current span: Analogue value (20,000 – 4,000 = 16,000)
- Offset analogue value (4...20 mA to 0...16 mA)
- Calculation: Delta of start point to end point (AEP – ASP = ∆A)
- Calculation: Factor for current to current in mA (∆A / 16 mA = factor)
- Multiplication of the current value (0...16 mA) with the factor
- Result of current value in mA
Calculation of the phase difference
To calculate the current asymmetry, the differential current between the individual phases (U-V, V-W and W-U) must first be calculated.
∆Motor current=motor current U-motor current V
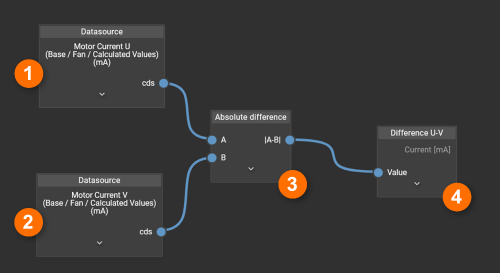
- Current value 1 of a current converter in mA, e.g. U
- Current value 2 of a current converter in mA, e.g. V
- Calculation of the absolute difference between phase U and V
- Current difference in mA
Calculation of the average current of the three phases
In order to be able to indicate the current asymmetry in %, it is first necessary to create a 100 % basis by determining the average value of the 3 phases.
Average current = (motor current U + motor current V + motor current W)/3
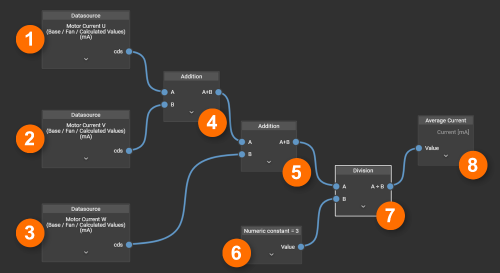
- Current value U in mA
- Current value V in mA
- Current value W in mA
- Addition of the current values of U and V
- Addition of the current value of W
- Constant number of phases = 3
- Division of the total current by the number of phases
- Result of the average current in mA
Calculation of the current asymmetry
The current asymmetry in percent is calculated from the current differences (U-V, V-W and W-U) and the average current of all three phases. This value is required for creating limit values in this use case.
Current asymmetry = (∆motor current)/(average current) * 100%
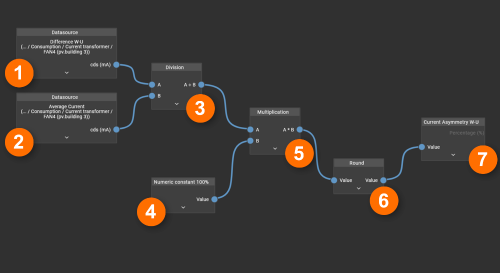
- Current difference U - V in mA
- Current average U - V - W
- Current difference divided by average current
- Constant 100%
- Ratio of current difference to current average multiplied by 100%
- Rounding the result to 1 decimal place
- Output of the current asymmetry in percent