Demand-oriented maintenance saves costs
Automated lubrication system for 1,000 kilometres of transport infrastructure
Remote maintenance
over long distances
Early maintenance alarm
Save money through demand-oriented
maintenance and reduced downtime
Results
- Higher uptime thanks to automated lubrication
- Manual maintenance significantly reduced
- Early alarm in case of low lubricant levels
- Very high downtime costs are reliably avoided
The challenge
The products are transported by a large overland conveyor system. The belt systems must always be well lubricated to ensure smooth operation of the conveyors. In the past, the mechanical lubrication systems featured non-electronic valves and mechanical timers, applying lubricant to the components at regular intervals of a few hours.
Lubrication occurred regardless of whether this was necessary or not, risking over- or under-lubrication of the system. An employee had to check the lubricant level at regular intervals, driving many kilometres along the conveyor each time. To avoid these disadvantages, they were looking for an automated and monitored system.

The solution – why ifm?
Our customer has launched a project as a way of differentiating themselves from their competitors. As part of this project, an automated lubrication system was to be implemented to reduce manual maintenance efforts to a minimum. The new system was to dispense the lubricant only when needed.
Looking for a suitable automation solution, they decided to work with ifm. One of the main reasons behind this decision was that ifm offered the ‘full package’ unlike other suppliers, who, for example, were able to provide a control system but no matching sensors. ifm’s solution is based on a SmartPLC with integrated AS-Interface Ethernet/IP gateway, to which all components are connected. It came with all the required accessories, such as power supply units and cables.
Especially the AS-i system integration is a major advantage for them, as it makes it relatively easy to reliably connect the devices despite the long distances. The new solution allows to record various data such as the number of cycles of the conveyor lubrication system. In addition, it measures the speed of the conveyor to make sure that lubrication only takes place when needed.
The SmartObserver software is used to record the essential parameters and report them to higher-level systems. In addition, an alarm is triggered when the lubricant supply in a container is running low. The new solutions helps to avoid unplanned downtimes that would cause costs in the single-digit million-euro range.
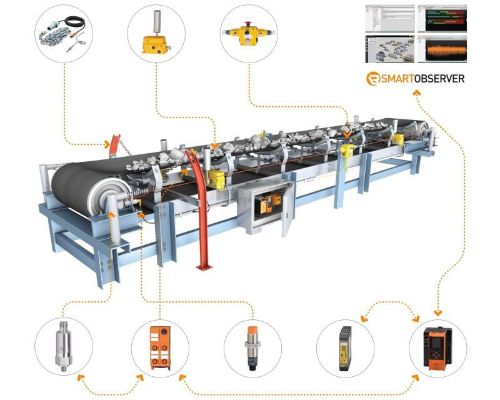