High availability in bulk material handling
Vibration monitoring on the bucket wheel drive
Transparency
Reduced
set-up times
Increased
machine availability
Results
- Vibration diagnosis of drive components
- Maintenance requirements are detected in time
- Reduction of unplanned downtime
- High availability
The challenge
Conveyor belts transport the ore to the stockpiles and also back to the cargo ships. For this purpose, so-called stacker-reclaimers or bucket wheel reclaimers are used. The combined stacker and reclaimer equipment picks up the ore with a large bucket wheel rotating above the bulk material. The bucket wheel drive technology is a critical part of these machines. Unplanned breakdowns, which have occurred in the past, sometimes necessitated lengthy repairs.
The reason for this was that there was no possibility of real-time maintenance. In the past, unusual vibrations in the drive technology were detected too late or not at all. The long maintenance times thus had a negative impact on the productivity of the entire system and resulted in high costs. To increase the availability of the bucket wheel reclaimers, the motor and gearbox vibrations were to be monitored in real time to enable an immediate response in the event of an impending fault.
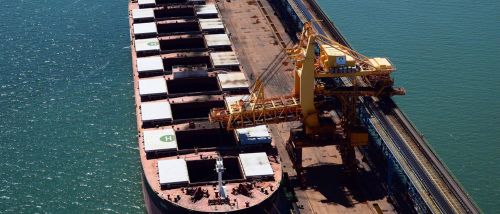
The solution – why ifm?
The port operator has a long-term cooperation with ifm. Against this background, ifm was able to develop a customised solution based on the requirements right at the start of the project. The reliability and quality of the solution were immediately convincing. Now vibration sensors of the type VSP001 are mounted on the drive technology and the recorded data is evaluated in real time by a VSE151 diagnostic electronics. In addition, sensors of the type TS2229 together with the TP9237 evaluation electronics detect the temperatures at the critical components.
Overall, a very good and transparent picture of the condition of the critical drive components on the machines is provided. As a result, maintenance measures can be better scheduled, avoiding unplanned machine downtimes as far as possible. The overall equipment efficiency is increased by monitoring and diagnosing the machine’s condition. In view of being able to evaluate the vibration diagnosis data even better, the IIoT platform moneo RTM is currently being tested. In this context, also additional systems with inductive or optical sensors are installed. For the future, the port operator expects a considerable reduction in unplanned maintenance measures due to equipment breakdowns.
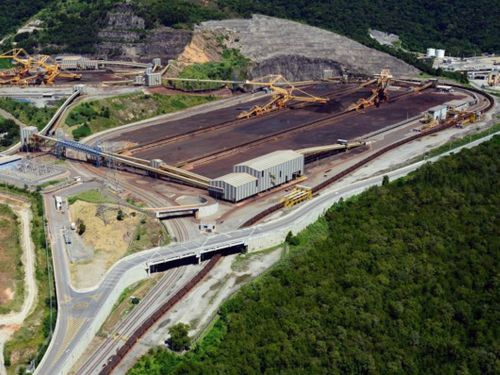