Bedarfsorientierte Wartung spart Kosten
Automatisiertes Schmiersystem für 1.000 km Transportinfrastruktur
Fernwartung über große Entfernung
Frühzeitige Alarmierung zur Wartung
Kostenersparnis durch
bedarfsgerechte Wartung und weniger Ausfälle
Ergebnisse
- Automatische Schmierung sichert die Verfügbarkeit
- Manueller Wartungsaufwand deutlich reduziert
- Frühzeitige Alarmierung bei niedrigem Füllstand
- Sehr hohe Ausfallkosten sicher vermeiden
Die Herausforderung
Der Transport der Produkte geschieht durch ein großes System, das aus Überlandförderern besteht. Die verwendeten Förderbandsysteme müssen stets gut geschmiert sein, um die reibungslose Funktion der Anlagen sicherstellen zu können. In der Vergangenheit arbeiteten die mechanischen Schmiersysteme mit nicht-elektronischen Ventilen und mechanischen Timern. Auf diese Weise dosierten die Schmiersysteme in regelmäßigen Intervallen von einigen Stunden Schmierfett auf die entsprechenden Komponenten.
Da die Schmierung so unabhängig davon geschieht, ob dies überhaupt notwendig ist, kann es zur Über- oder Unter-Fettung des Systems kommen. Eine weitere Folge dieses alten Systems: Ein Mitarbeiter muss regelmäßig den Füllstand des Fetts prüfen und dazu viele Kilometer entlang des Fördersystems mit dem Auto zurücklegen. Um diese Nachteile zu vermeiden, war unser Kunde auf der Suche nach einem automatisierten und überwachten System.

Die Lösung – warum ifm?
Mit einem Projekt versucht sich die Firma als Marktführer von den Wettbewerbern zu differenzieren. In diesem Rahmen sollte auch ein automatisiertes Schmiersystem realisiert werden, um insbesondere den manuellen Wartungsaufwand zu reduzieren. Das neue System soll das Fett für das Fördersystem bedarfsgerecht dosieren.
Bei der Suche nach einer passenden Automatisierung haben sie sich für eine Lösung von ifm entschieden. Ausschlaggebend für diese Entscheidung war vor allem das Komplettangebot. Im Gegensatz zu anderen Anbietern, die beispielsweise eine Steuerung aber nicht die passende Sensorik liefern konnten, hat ifm eine komplette Lösung angeboten. Diese basiert auf einem SmartPLC mit integriertem AS-Interface Ethernet/IP-Gateway, an den sämtliche Komponenten angebunden sind und auch alle Zubehörteile wie Netzgeräte und Kabel waren bereits in der Lösung enthalten.
Gerade die Einbindung eines AS-i Systems war ein großer Pluspunkt, da es so relativ einfach ist, die Geräte trotz der großen Entfernungen sicher anzubinden. Mit der neuen Lösung können verschiedene Daten wie die Anzahl der Zyklen des Förderschmiersystems aufgezeichnet werden. Auch die Geschwindigkeit des Förderers wird gemessen, so dass nur geschmiert wird, wenn dies tatsächlich notwendig ist.
Als Software ist der SmartObserver installiert, der die wesentlichen Parameter aufzeichnet und an übergeordnete Systeme weitermeldet. Zudem wird ein Alarm ausgelöst, wenn der Fettvorrat in einem Behälter zur Neige geht. Unser Kunde verhindert so ungeplante Stillstände, die Kosten im Millionenbereich verursachen würden.
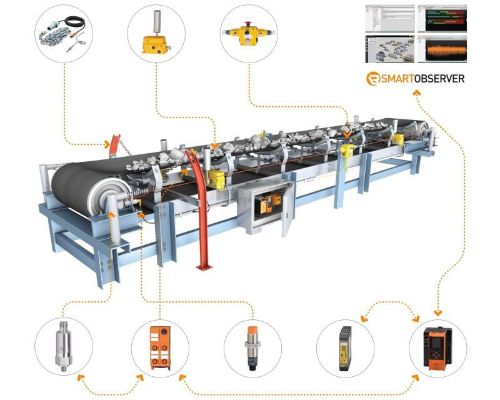
Weitere Bilder, falls vorhanden