Metering, visualisation and analysis of electrical energy using energy meters with Modbus TCP interface and moneo RTM
Companies are increasingly focusing on production-level energy monitoring to allow for more efficient, sustainable and forward-looking planning. Information about possible reactive currents can be used to implement suitable solutions for reactive power compensation and thus avoid unnecessary costs. For this purpose, energy meters are used.
Measuring energy consumption
In the production process, sensors are mechanically finalised at an assembly island before being put through the quality assurance process. At the assembly island, more and more IT components are required to satisfy the growing demand for digital support in the assembly process and to record and provide order-related data. This passive production equipment accounts for an increasingly significant portion of total energy consumption.
The starting position
Measures to save energy and optimise energy consumption can only be effective if the energy requirements are known in detail. Each energy meter your supplier uses to bill electricity consumption can help to obtain an overview. But when it comes to evaluating the efficiency of energy-saving measures, existing solutions have been inadequate so far:
- Meter readings reveal little to nothing about how effective individual measures are because there too many influencing factors
- The effectiveness of optimisation and energy-saving measures can only be determined when put in relation and cannot be considered in absolute terms
- For example, if the number of items produced decreases during the same period in which a measure was introduced, it cannot be clearly determined whether the measure had any effect
- Manual recalculation in order to obtain usable information is nearly impossible or too time-consuming
Goal of the project
Digital recording of energy consumption
The prerequisite for any energy-saving and optimisation measures is to digitally track the energy consumed by dividing production into meaningful areas. Energy transparency increases awareness of energy usage, ensuring a more careful use of electricity and thus reducing costs.
Integrating moneo RTM makes it possible to:
- measure energy consumption by process/work area
- centralize information on energy consumption
- derive consumption values:
– total consumption
– peak consumption
– base load consumption / standby
– consumption during non-production time
– reactive currents and reactive power produced - calculate the cost of energy consumption in the scaled area
Implementation
Energy metering via Modbus TCP with LR Agent and moneo RTM
The assembly island uses a three-phase supply (L1, L2 and L3). In these supply lines, a three-phase energy meter with Modbus TCP interface was installed. LR Agent enables reliable reading of the required Modbus registers. In moneo RTM, the values are monitored and analysed and consumption costs are immediately calculated.
Success
Identify base load costs to derive energy-saving measures
Transparent energy consumption with moneo RTM
- Indicates the total power consumption
- Indicates the current power consumption
- Indicates the current voltage, current and power for all three phases
- Indicates the current reactive currents and reactive power produced
- Indicates the total reactive currents and reactive power produced
- Enables calculation of total costs via ‘Calculated values’
- Enables calculation of current costs via ‘Calculated values’
System structure
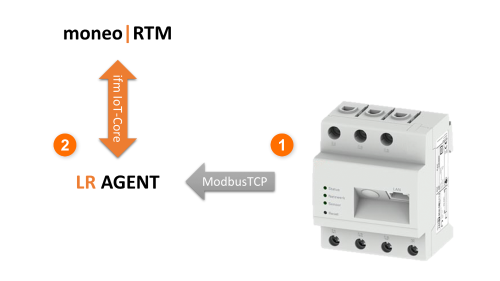
- Siemens 7KT1260 energy meter
- LR Agent
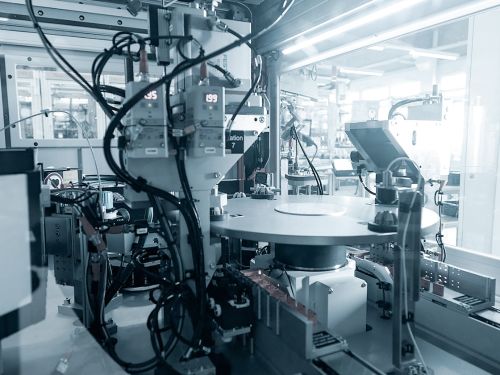
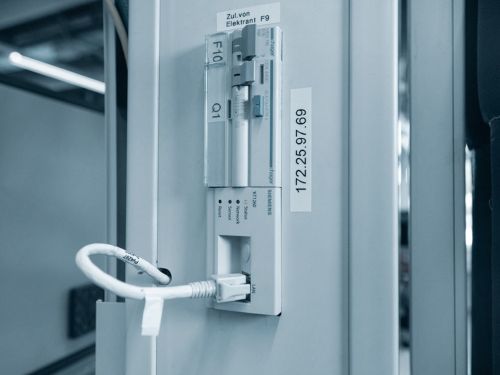
Dashboard
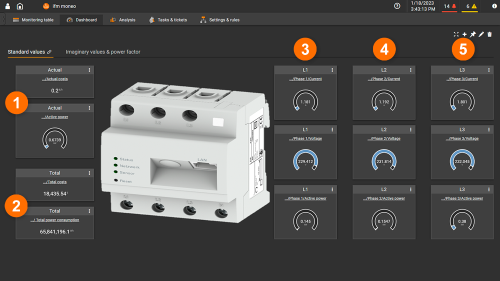
- Current costs per hour + current power requirements
- Total costs + total power requirements
- Phase 1 (L1): current measured current, voltage and power values
- Phase 2 (L2): current measured current, voltage and power values
- Phase 3 (L3): current measured current, voltage and power values
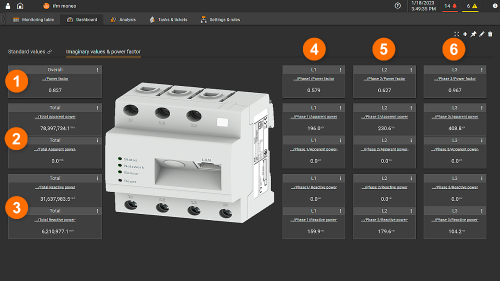
- Overall power factor
- Total apparent power (+/-)
- Total reactive power (+/-)
- Phase 1 (L1): current power factor, apparent power and reactive power
- Phase 2 (L2): current power factor, apparent power and reactive power
- Phase 3 (L3): current power factor, apparent power and reactive power
Analysis
The analysis function allows the user can access history data and compare different process values. The diagram shows the power consumption and the correlating costs over time.
- Weekend (standby) ①
- Night shift ②
- Early shift ③
It can be seen that there is a base load of 0.3 kW during standby at the weekend, which results in costs of approx. 0.9 cents per hour. While this doesn’t sound like much, it adds up to about €2,150* over the course of a year. Especially in this passive area without active value creation, measures that reduce the need for energy can have a noticeable effect on total costs.
The diagram also reveals a clear difference between the night shift and the early shift. For example, if production takes place 24/7 on weekdays, costs could be reduced by using multi-tariff agreements (day rate/night rate) and corresponding task schedules for the different shifts. Consequently, energy-intensive equipment, such as the Binder furnace, could be operated more intensively during low-rate periods, while reducing its use during high-rate periods.
* 1 weekend = 46 h of production-free time
1 year = 52 weeks ≈ 52 weekends
0.9€/h * 46h * 52 = €2,152.80
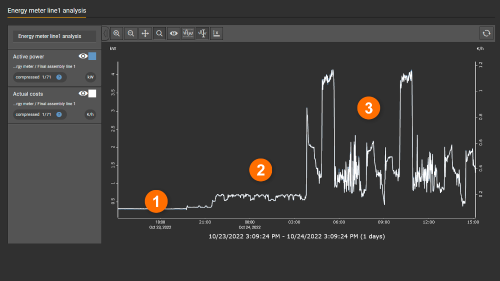
- Blue = current consumption (mostly overlaid by identical value)
- White = current cost per hour
Calculated values
The measured variables provided by the energy meter in the Modbus registers are read using LR Agent and booked into moneo. However, they do not always appear in the desired unit. Power values are typically expressed in kW. The standard SI unit is Watt, which is also used in the registers. Using a ‘data flow’ function, the input variable (W) can be converted into the desired unit (kW).
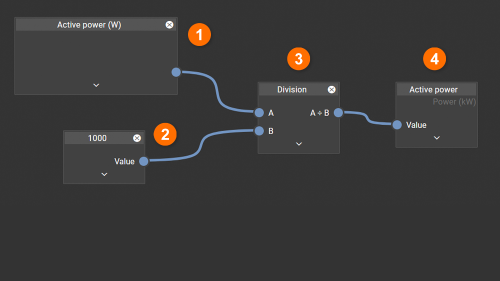
- Active power in W
- Constant: divisor for conversion to kW
- Division
- Active power in kW
Equally helpful for evaluating and analysing the consumption values is to calculate the costs of power consumed. These are usually billed by the energy supplier in kilowatt hours. The basic parameter used for this calculation is the input power converted into kilowatt hours in the previous data flow. Two data flows are created:
Cost calculation of current power consumption
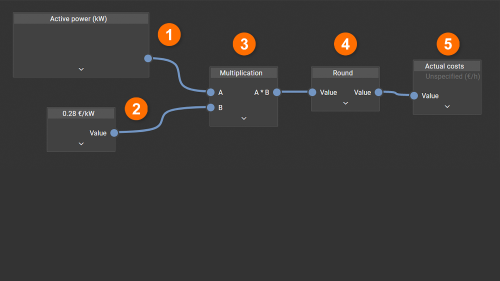
- Active power in kW
- Constant: cost per kilowatt hour
- Multiplication
- Rounding to 2 decimal places
- Current costs per hour
Cost calculation of total power consumption
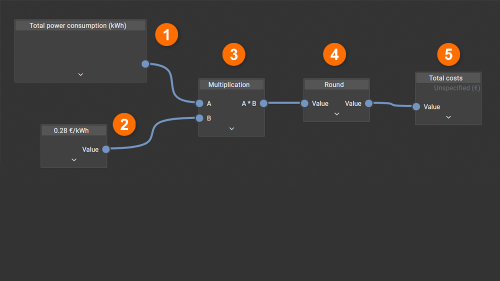
- Current costs per hour
- Constant: cost per kilowatt hour
- Multiplication
- Rounding to 2 decimal places
- Total costs