Continuous condition monitoring of a decanter in the wastewater industry
Kressbronn wastewater treatment plant
The end result of the wastewater process in a wastewater treatment plant is "clean water". The "primary sludge", which cannot be further purified, is produced during the cleaning process. It is disposed of as special waste in an incineration plant. The cost of disposal for special waste is determined by weight. Since water makes up the majority of the weight in the untreated primary sludge, it is very much in the interest of treatment plants to separate the solid and liquid parts to reduce the weight. There are various methods for doing this.
The method used in the Kressbronn wastewater treatment plant is a decanter. In this process, water is separated from solids by means of centrifugal force. The liquid part of the primary sludge is directed back to the treatment process and the remaining dry part of the sludge is disposed of.
Unplanned downtime could have severe repercussions, potentially disrupting the entire municipal wastewater disposal system and in the event of an extended failure even causing a complete halt to its operations.
The starting position
The decanter was not continuously monitored and the bearings were not replaced until after damage had become audible. In the worst case this could lead to an unplanned system stoppage, which in turn would cause an accumulation of the primary sludge and, if repairs took an extended time, to an interruption in the operation of the wastewater treatment plant.
No condition monitoring of the drum motors.
Maintenance intervals according to defined patterns.
No alarm system or early warning when damage is beginning.
Goal of the project
Introduce continuous monitoring of parameters relevant to the process and plant.
Organise servicing measures for critical plant parts such as the gear to prevent unplanned downtime.
Implementation
The decanter used in Kressbronn is already several decades old and is controlled by a Siemens S5 PLC. This makes it difficult to supply the various parts of all components and it is practically impossible to integrate process monitoring components directly into the PLC. To achieve the longest possible availability of the decanter and especially of the critical components despite this, these components were equipped with vibration and temperature sensors.
Monitoring
- The bearing of the centrifuge
- of the drive motors
- of the gear
The speed of the two motors is measured by two IFC201 inductive sensors. All sensor data is transferred to three VSE150 units installed in a control cabinet.
For a modernisation anticipated in the future and to convert from an S5 PLC to an S7, VSEs with ProfiNet interfaces were used. This makes it possible to incorporate vibration parameters directly into the controller of the decanter.
To provide the customer with visualisation that is easy to operate and adapt, moneo was used for this purpose. It offers the advantage that additional sensor data of the entire plant can also be integrated into a system. A system of alarms is also provided if the set limit values are violated.
Success
Successful retrofit of a machine that is several decades old and for which spare parts procurement is becoming more and more difficult. The additional monitoring will make it possible to continue operating the plant safely and reliably for many more years.
Dashboard
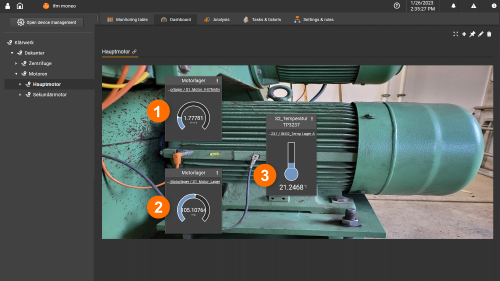
- V-effective of main motor bearing [mm/s]
- Vibration of main motor bearing [mg]
- Bearing temperature of main module [C°]
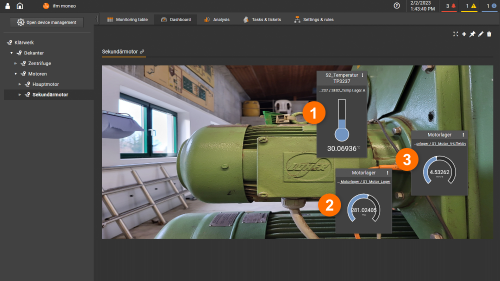
- Bearing temperature of secondary module [C°]
- Vibration of secondary motor bearing [mg]
- V-effective of secondary motor bearing [mm/s]
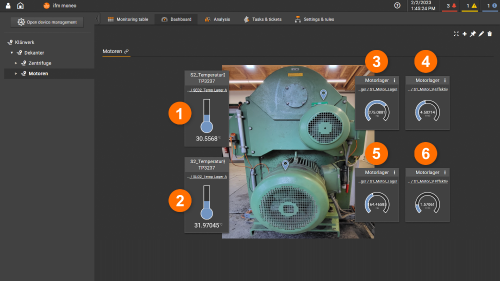
- Bearing temperature of secondary module [C°]
- Bearing temperature of main module [C°]
- Vibration of secondary motor bearing [mg]
- V-effective of secondary motor bearing [mm/s]
- Vibration of main motor bearing [mg]
- V-effective of main motor bearing [mm/s]
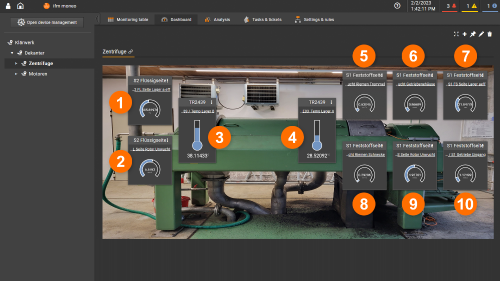
- a-effective of bearing on liquid side [mg]
- Imbalance of rotor on liquid side [mm/s]
- Bearing temperature on liquid side [C°]
- Bearing temperature on solid side [C°]
- Imbalance of drum belt [mm/s]
- Imbalance of gear housing [mm/s]
- a-effective of bearing on solid side [mg]
- Imbalance of screw belt [mm/s]
- Imbalance of rotor on solid side [mm/s]
- Vibration at gear input [mm/s]
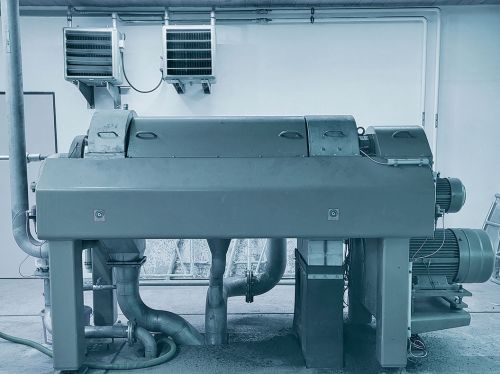
Our customer
The municipalities of Kressbronn a. B. and Langenargen jointly operate a wastewater treatment plant in Eichert. Wastewater is treated in four stages at the wastewater treatment plant: Mechanically, biologically, chemically and with powdered activated carbon. The fourth treatment stage is particularly important as it filters trace elements (e.g. drug residues) out of the wastewater. After the wastewater has passed through all four treatment stages, it is finally discharged back into Lake Constance.